Modern condition monitoring opens new opportunities to optimise how and when we use skilled resources onsite. The ability to efficiently monitor an entire fleet of machines in real-time rather than manually checking them on a monthly or quarterly schedule can change a manufacturer’s entire maintenance process – for the better.
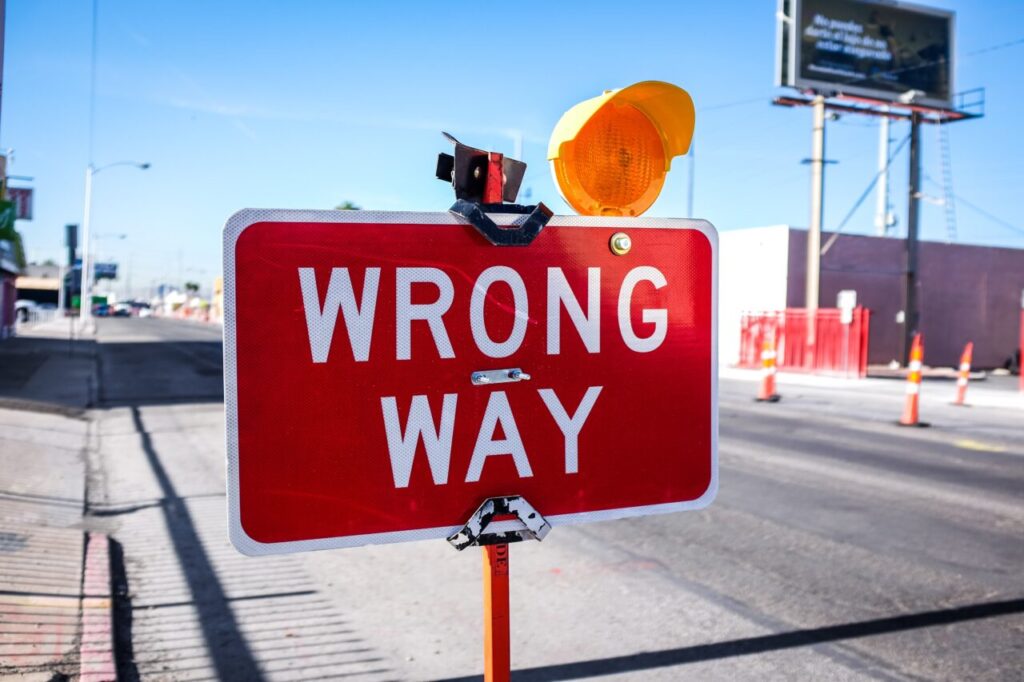
Unplanned downtime costs industrial manufacturers an estimated $50 billion USD each year, according to Deloitte. Machine condition monitoring, when done effectively, has the potential to increase efficiency, reduce expensive downtime, and boost productivity in manufacturing.
Yet, some manufacturers are hesitant to make the transition, even though the benefits seem clear. Let’s have a look at why there may be a bias in the industry and what factors are leading manufacturers to take a closer look at online condition monitoring solutions.
In this article, we’ll explore:
- Why the manufacturing industry leans toward manual methods
- The challenges created by manual machine inspection and analysis
- Hidden costs of manual maintenance inspection and analysis
- The expansive scope of online condition monitoring solutions
- The difference between condition monitoring and vibration analysis
Why the manufacturing industry leans toward manual methods
Companies are often focused on growth and increasing revenue, both of which are valuable goals. However, it’s also critical to review your operations to see where you can cut costs, reduce risk, and prevent loss to your company.
Here are a few reasons why the industry has been slow to capitalize on the benefits of online condition monitoring:
- We have decades of history of doing things a certain way
- Training commonly focuses on understanding manual analysis methods
- Manual inspection and analysis is the safe and known way of working
- A disconnect exists between those identifying issues and those able to champion change
- Other initiatives and spending create competition for internal resources
- It’s challenging to get enough perspective to see how current processes fall short
- Past alternatives may have been cost-prohibitive, so the ideas were not revisited
Exploring why your company does things a certain way, what it costs to maintain the status quo, and what costs you could reduce or mitigate with alternatives is an excellent way to strengthen your business for the long term.
Challenges created by manual machine inspection and analysis
For decades, machine inspection and maintenance were done manually, with heavy reliance on having the manpower to physically inspect and collect data from machines. This manual process could include travel to remote worksites, manual inspections, and travelling with samples to assess what was happening on site.
These processes still exist today in many manufacturing companies. Many organizations schedule maintenance activities on a monthly or quarterly basis, and it’s up to maintenance staff to try to inspect every machine to keep things in peak condition and avoid expensive failure, breakage, downtime, and repairs.
While hands-on monitoring was effective years ago, companies still relying on this approach to keep their machines running are facing increasing challenges. Often, the human resources available for inspection and maintenance simply can’t meet the demand for manual analysis.
The manufacturing workforce is grappling with change, and companies need to adopt new thinking to attract workers to manufacturing roles. The scope of the work often is too great for maintenance teams to complete to avoid failure and breakage. Worse, teams don’t have the chance to get ahead by anticipating the maintenance needed to avoid machine failure or worn-out parts in the first place.
Hidden costs of manual maintenance inspection and analysis
The challenges created by manual analysis methods cost companies money – and lots of it. How? Downtime is expensive, and so are rush jobs to complete critical repairs. Parts can be hard to procure quickly, and to pay to warehouse an array of them in case of need isn’t a viable solution, either.
If maintenance teams must constantly react to issues after they happen, they can’t effectively inspect or monitor other equipment, leading to costly and preventable repairs. There’s also a significant cost to having employees do all the work manually, travel to remote sites, and manage lab samples.
If more companies could put a number on what they lose to parts failure and machine breakdown in a year, stopping that financial waste would become a high priority. The problem is that many companies simply don’t have a handle on what downtime or unnecessary repairs are costing them.
The expansive scope of online condition monitoring solutions
Over time, solutions have been developed that allow maintenance managers to go beyond manual analysis and data collection and explore online condition monitoring. Comprehensive monitoring in real-time allows you to do maintenance on your terms instead of responding to critical matters after they happen.
While alternatives may have seemed costly years ago, technology now offers far more value for a much more affordable price. The scope of what you can do with online condition monitoring systems is far greater, which expands your ability to protect yourself from unnecessary waste, loss, or costs.
Condition monitoring versus vibration analysis
Alternatives that combine both condition monitoring and vibration analysis provide far more data, insight, and control over outcomes. How do these two elements work together to support production and uptime?
- Condition monitoring: Condition monitoring is broad in scope, allowing you to monitor your entire fleet of machines in real-time to ensure you always know what’s happening onsite. This type of monitoring will alert you when something goes wrong, no matter how difficult or remote the machine is to reach.
- Vibration analysis: Vibration analysis goes beyond monitoring to tell you what is wrong with a particular machine, giving you in-depth insights into what’s happening and what you need to do to respond appropriately.
Modern online systems provide more tools than traditional options and allow industry professionals to focus on highly-skilled responses rather than spending time on routine tasks. They provide you with the ability to monitor every machine, not just for failure, but to analyse what is wrong and what to do to increase uptime.
Understanding the new tools and creating a new monitoring process from the inspection process requires rethinking from all levels of management–but it can have a big impact on your bottom line. Manufacturers can be ready for these transitions as they develop simply by questioning the status quo and breaking down the value of a new solution.
Machine condition monitoring can be done better, and solutions exist to support your company in making the shift. With daily and historical data, you’ll be able to determine the best timing for maintenance and repairs and gain control over your equipment.
Condence provides online and remote monitoring tools to help you transition from time-consuming legacy processes to a more modern approach. Contact us to book a demo.
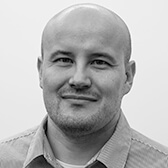
Panu Kinnari
Chief Operating Officer
panu.kinnari@distence.fi
0 Comments