Megger acquires Distence – expanding our predictive maintenance capabilities
We’re delighted to share some exciting news with you: Megger, a global leader in testing and diagnostics equipment, has acquired Distence. Effective immediately, Distence will become part of the Megger family, and we are thrilled about the opportunities this will bring. This acquisition will allow us to combine the strengths
New Condence.io partner Micron Eagle Hydraulics to Integrate Industrial Functional Fluid Monitoring
Micron Eagle Hydraulics Ltd., is a leading provider of hydraulic systems, components, repairs, and fluid conditioning in the UK. Through this collaboration, Micron Eagle has integrated Distence Ltd. Condence.io remote monitoring platform with its innovative “Fluid Fitness Technology”. Leveraging the core capabilities of the Condence.io platform allows Micron Eagle to
Understanding the true value of AI to industrial maintenance
Downtime is expensive. Effective monitoring solutions for industrial maintenance can reduce downtime and give your company a competitive advantage in managing your assets over the long term. However, understanding what artificial intelligence (AI) and machine learning concepts mean to an organisation can be a challenge. Many opinions and expectations exist
Coe the reliability assistant: The Future of Prescriptive Maintenance
Prioritize machinery that genuinely demands attention. As data sets grow, their complexity often leads to confusion and inefficiencies. Access topertinent, comprehensible, and actionable detail is a significant challenge. Enter Coe, thedigital co-engineer from Distence, the creators of condence.io, that’s here to revolutionizeprescriptive maintenance. By focusing on rotating machinery – a
Industrial gearbox with potential gear issue – Detected by Condence Coe
In this case, the customers industrial gearboxes were manually monitored as part of their normal maintenance program. This process was, however, time-consuming, hard to scale, and costly. The customer was looking for a more efficient and effective solution. This example is built using data from a real gearbox case that
Recent Posts
- Megger acquires Distence – expanding our predictive maintenance capabilities November 11, 2024
- New Condence.io partner Micron Eagle Hydraulics to Integrate Industrial Functional Fluid Monitoring January 31, 2024
- Understanding the true value of AI to industrial maintenance September 29, 2023
- Coe the reliability assistant: The Future of Prescriptive Maintenance August 2, 2023
- Industrial gearbox with potential gear issue – Detected by Condence Coe April 19, 2023
- Industrial fan with a bearing failure – Detected by Condence Coe April 19, 2023
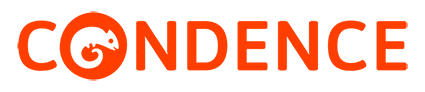