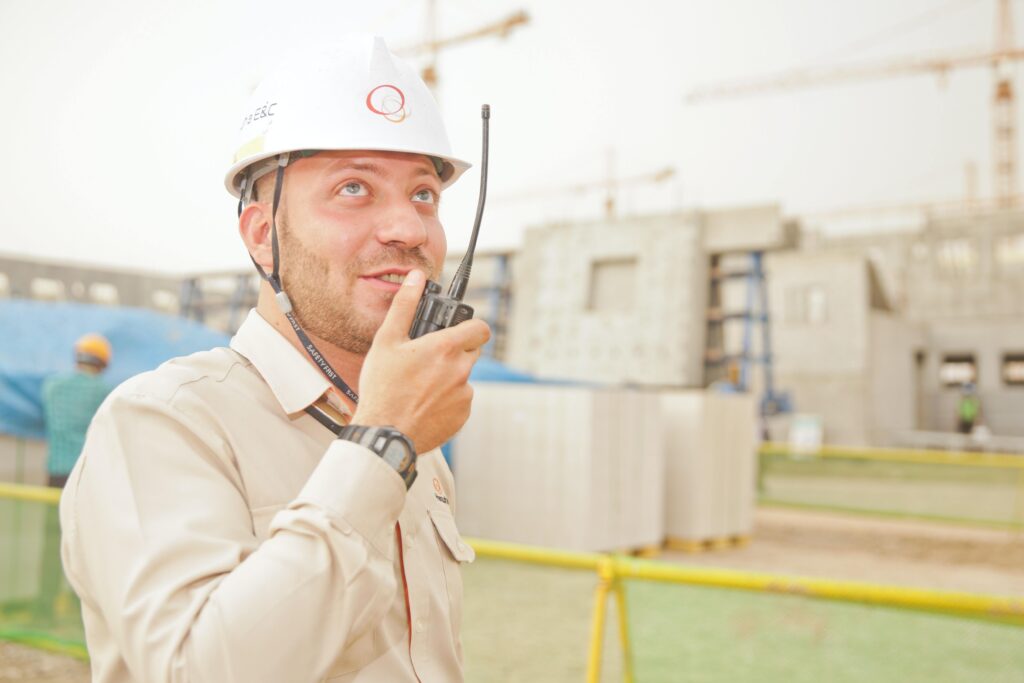
How would you describe your company’s current approach to machine maintenance? Perhaps you’re primarily focused on scheduled maintenance for your most expensive machinery to avoid costly unplanned downtime. While this is an essential part of keeping your facility up and running, it’s also important to be aware of your equipment’s
failure patterns and the real-time status of parts like pumps and bearings.
Having a good idea of how these smaller components are performing is key to understanding your machines’ true status. These insights will allow you to monitor your assets more closely and will let you know early on when to take action through maintenance or repairs. In this blog post, we’ll discuss how to track machine failure patterns to avoid downtime.
Defining and understanding machine failure
When we talk about failure, we mean not only the machine’s final failure when it’s time to replace the equipment altogether, but all of the smaller failure patterns and issues that occur throughout its life cycle. These complexities of machine health add many challenges to your daily work as you manage your plant’s operations.
Precision maintenance has been proven to maximise productivity uptime and ROI, making it superior to a reactive approach or mere scheduled maintenance. Despite this knowledge, reactive and scheduled maintenance remain common.
Instead, it’s best to take a proactive approach that considers all of your operating machinery at various levels. This will ensure your maintenance efforts are robust enough to keep your facility and daily operations running smoothly. Otherwise, you’ll be left vulnerable to missing timely signs of breakdowns.
Why smaller failures matter: the road to complete breakdowns
Smaller failures matter in terms of the bigger picture. For example, a pump-motor set can have hundreds of components. This sheer amount significantly increases the variety of possible failure patterns and the probability of possible failure patterns. In fact, pumps are five times more likely to fail or exhibit failure patterns than other comparable parts.
Corrosion, fouling and wear are a few of the common issues that lead to pump failure. We know these problems can be reduced by selecting high-quality pumps that suit your operations’ specific needs. However, you can also prolong your pump’s life and maximise your value for money by monitoring the components closely, staying up-to-
date with even minimal changes in pump performance or condition.
This can be done with a data-based solution that provides insights into factors like turbulence, deterioration of wear rings and erosion. Use precise data-based monitoring to inform your maintenance approach and you will slow down your pump’s wear rate and increase your return on investment.
When it comes to preventing fouling, cleaning is the ticket to improving your pump’s efficiency and capacity. Monitoring by collecting data on your facility’s pumps will ensure you take the right action at the right time, whether that means cleaning components or conducting another form of maintenance.
Bearings are another part of your production equipment that you’ll likely handle on a regular basis. In general, bearings are designed to last for approximately 10 years, yet they are the most commonly replaced part and rarely live out their 10-year life cycle. This is likely due to improper lubrication, contamination and any issues that can affect
the oil or coupling alignment. In fact, about 80% of bearing failures can be attributed to improper lubrication.
Bearings may not be the most expensive or difficult parts to replace, but taking steps to monitor a part more closely and prolong its life is always a better investment than replacing it altogether. You can monitor bearings precisely with a solution such as a lubrication indicator to avoid further and more detrimental problems, including improper operating temperature. This will allow you to hone in on friction-related issues when the standard solution of greasing your bearings does not work.
Pinpointing failure patterns for a robust maintenance strategy
Taking a robust approach to maintenance that factors in smaller machine failure patterns rather than solely focusing on the large machines and complete failure is an excellent way to avoid costly unplanned downtime. Ideally, you’ll want to know immediately when a failure pattern, big or small, is on the horizon.
In the case of pumps, there are different failure modes depending on your pump’s design. Because of the numerous failure possibilities, production managers need to understand exactly how their equipment is failing, not just that it is failing.
In the case of bearings, consider that a great deal of time and effort can go into bearing lubrication at a steel mill, for example. If the facility’s condition monitoring team doesn’t have the human resources to monitor every individual bearing at the plant, a technician must resort to greasing in a preventative manner. This technician is potentially wasting time checking bearings that do not need greasing at all. Another possibility is that lubrication only seems to be the problem, but after the technician has greased the bearing, the issue persists.
In this instance, a lubrication indicator would have saved time and manual labour by providing data insights to pinpoint the real root of the problem. A smart solution would eliminate the need to manually monitor so many different factors, including vibration level noise level and ball bearing looseness.
Monitoring even standard equipment and more minor procedures like lubrication are crucial to a facility’s overall well being. This sort of monitoring can be done efficiently with a data solution.
Understanding and managing risks
By conducting precision maintenance and gathering insights into potential machine failures, both small and large, you’ll have a deeper understanding of the bigger picture at your plant—even when it comes to your less expensive equipment.
You’ll gain visibility into how the condition of your equipment and its parts may be affecting your production quality or snowballing into more significant and costly problems down the line. By tracking failure patterns, you’ll also be better informed when it comes to determining the risks you might want to take and when to take action before
any issues progress beyond repair.
Actionable data and smart solutions with Condence
We believe that data should be useful, not overwhelming. That’s why we provide the data that matters most to you as well as smart features that take daily and historical data into account to reveal significant changes that might otherwise go unnoticed.
Condence’s data-focused solution enables you to monitor your equipment in a way that helps you determine the optimal time to perform checks or conduct repairs. Our technology provides unlimited data collection, management and computing power, giving you back your human resources and saving you time. We deliver in-depth
analytics in an easy-to-understand manner so you can quickly determine which actions to take, when to take them and which of your team members should be involved.
Contact our team to book a demo and discover how Condence can help your organisation get the most value out of its machinery of all sizes and costs.
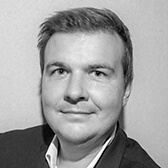
Janne-Pekka Karttunen / CEO
janne-pekka.karttunen@distence.fi