How precision maintenance maximises productivity uptime and ROI
As a plant production or operations manager, productivity and efficiency are your top priorities. Precision maintenance combined with data analysis makes these responsibilities more manageable, and enables you and your organisation to make more informed maintenance decisions.
What do we mean by precision maintenance? This concept comes from the idea of accurately pinpointing potential issues that signal the beginnings of anything from unexpected repair needs and downtime to catastrophic machine failure. Precision maintenance gives plant managers the information required to plan the best method of action, and helps them take that action at the optimal time.
In this blog post, we’ll cover:
● How precision maintenance can help you solve common maintenance challenges
● The benefits of leaving manual methods behind
● The importance of leveraging data to make better decisions for your company
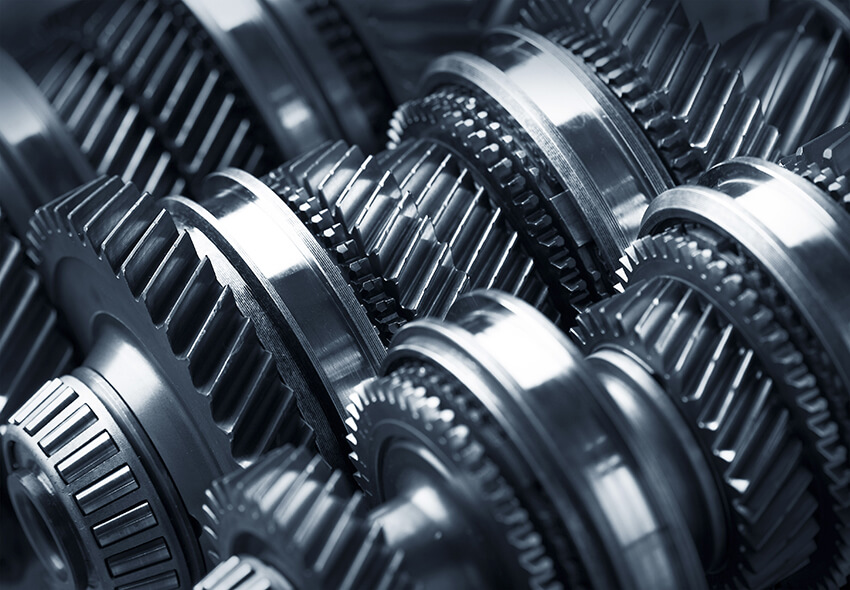
The traditional approach to industrial maintenance
Many companies in the energy, pulp and paper, steel and mining sectors still rely on manual maintenance and inspections. Although this is a longstanding practice, on average, only 8% of machinery is frequently inspected. This approach leaves a lot to chance in terms of unexpected downtime and faster machine deterioration.
With these risks in mind, it would be wise for plant managers to take a more proactive approach to industrial maintenance. However, with seemingly no systematic, data-backed way of determining when to inspect machinery or make repairs, these managers are left with a serious challenge.
Barriers to change
A reluctance toward investing in resources and technology, as well as a lack of awareness around precision maintenance methods can both be barriers to updating your maintenance approach. When asked about the main obstacles hindering their plant from improving maintenance methods, 48% of plant employees cited lack of resources or staff, while 38% cited a lack of understanding of new maintenance options and technologies.
However, relying heavily on mere routine check-ups often has costly consequences. It is well known by every operations and production manager that maintenance is crucial to machine health and the overall success of an industrial facility. In fact, maintenance costs account for 15 to 40% of total production costs according to Hans Löfsten, professor of Technology Management and Economics at Chalmers University of Technology.
With such a significant portion of a plant’s budget dedicated to maintenance, it’s imperative to take a cost-effective approach. A maintenance approach that lacks precision, or that relies on reacting to issues as they arise instead of trying to predict them, can result in prematurely ageing equipment and unplanned, costly downtime.
This reactive traditional maintenance method can often lead to repairing machinery once it has already failed or is beginning to fail, leaving little to no room for unexpected failures or monitoring machine wear and tear in between scheduled maintenance. Imagine the amount of energy and time that might be wasted when critical machinery requires extra downtime because you had no way of knowing the machine needed attention weeks or months before the usual scheduled time.
In fact, ageing machinery is the most significant pain point for operations and maintenance, followed closely by equipment failure. Fortunately, this is one of the major areas that precision maintenance is designed to address. Data-backed decision making for precision maintenance is essential for industrial sites because it allows plant managers to predict serious issues before they actually arise. Let’s explore how it works.
Addressing common challenges with precision maintenance
How does precision maintenance help production managers combat ageing machinery, equipment failure and the like? The foundation of precision maintenance is built around monitoring asset conditions and balancing your options.
This proactive approach to maintenance is essential to avoiding emergency shutdowns and ensuring that any shutdowns you do schedule are absolutely necessary. However, keep in mind that downtime needs to be planned well in advance and aligned with your production schedules to minimise production and revenue loss.
Overcoming common maintenance challenges is where precision maintenance and data come into play. By using data collection and analysis to monitor machine conditions in real-time, and predict downtime and repair needs, managers can use plant resources more wisely and delegate responsibilities to staff more effectively.
With precision maintenance software and hardware that automatically and consistently collects and analyses useful data, production managers can go far beyond the limitations of a computerized maintenance management system that only offers a small portion of the required data often collected manually, and stored in an unsystematic way that makes data insights challenging to gather.
Instead, data-backed precision maintenance operates on a system that can be monitored remotely; and plant managers already possess the skills and knowledge needed to adjust notifications and schedule maintenance and repairs in an optimal way.
Hardware and software for easy precision maintenance
Industrial machine maintenance often requires specialised skills and knowledge. If there aren’t enough people on your team with these skills, it creates a significant obstacle as you work to improve your maintenance strategy.
Below are three examples of how using data to collect real-time information about your machinery can alleviate the need for these specialised skills. Leveraging data makes precision maintenance easier and allows you to monitor the condition of individual parts closely.
1. Software
Precision maintenance software solutions collect and analyse data. Using the cloud and embedded edge-analytics, production and operations managers have access to data visualisation tools and various widgets, allowing them to monitor and customise how their data is delivered in an accessible way.
The software is always listening, safely and securely collecting relevant data even outside of regular work hours. It is also highly customisable, allowing managers to set specific notifications for the condition thresholds that best suit their team and their facility.
2. Application: Gearbox condition monitoring
A common, complex and essential component for many industrial facilities, gearboxes are manually inspected manually and quite often. But the way they are monitored is not ideal because facilities typically only collect the data they gather during each manual inspection. This limited view can lead to huge oversights. Instead, gearboxes should be monitored constantly to avoid unexpected downtime or failure.
Through continuous monitoring of several methods including oil condition, in-depth vibration analysis and temperature, managers can gain insights into early signs of wear, changes in oil quality and whether the gearbox is being used efficiently in terms of running hours.
3. Application: Compressor condition monitoring
There are many different types of compressors, so your solution needs to have multiple options for sensors and vibration analysis as well as customisable terminals to ensure that each manager can find a condition monitoring set up that suits their specific needs.
Compressor condition monitoring delivers metrics to help detect signs of wear, user errors, temperature changes and more to help you combat machine ageing and, of course, avoid unscheduled downtime.
Your partner in machine health
How exactly does precision maintenance impact an industrial facility? In terms of cost, the average direct savings cover four months of running a solution like Condence.io.
Monitoring conditions in real-time through precision maintenance instead of relying on traditional methods can reduce repair time significantly, decrease overall equipment effectiveness losses by nearly half, and save around €99,625 per failure, according to McKinsey.
At Condence, we can confidently say that we haven’t missed a single machine failure in 12 months. Through cloud and edge computing, our solution listens, collects and analyses data for plant managers to easily apply to their machinery and facilities.
Book a demo to discover how Condence can revamp the way your organisation approaches maintenance.
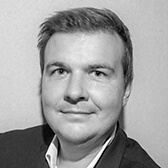
Janne-Pekka Karttunen / CEO
janne-pekka.karttunen@distence.fi
0 Comments