Organizations’ need to monitor the condition of their manufacturing and process machines has existed for decades. Still, while technological advances have driven other industries rapidly forward, machine condition monitoring hasn’t evolved at the same speed.
However, remote condition monitoring presents a new opportunity for both the industry and workforce to evolve in positive ways. Remote condition monitoring has been growing more sophisticated every year, and with it, the need for an increasingly skilled and educated workforce.
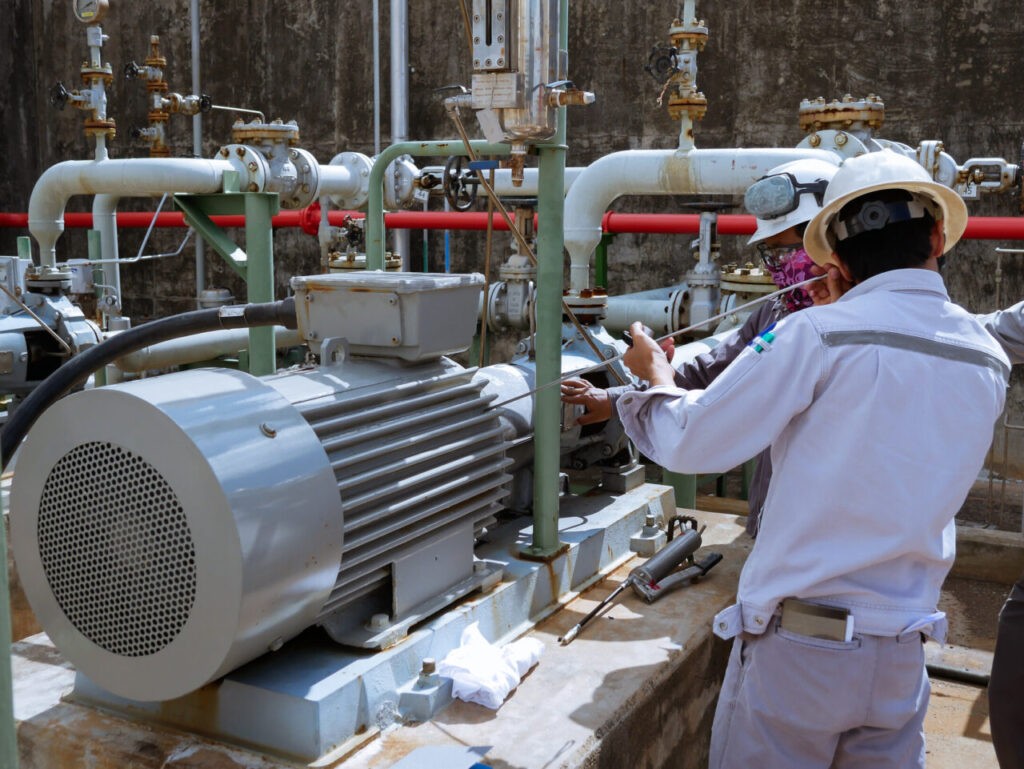
With remote condition monitoring, organisations can make significant progress towards cost efficiencies and decreased downtime. They can also attract new talent that will help drive positive change company-wide.
In this article, we’ll walk you through:
- How the condition monitoring industry has changed over time
- Why condition monitoring now offers high-end technical employment opportunities
- Attracting the right talent necessary to industry evolution
- Creating a culture of change
How the condition monitoring industry has changed over time
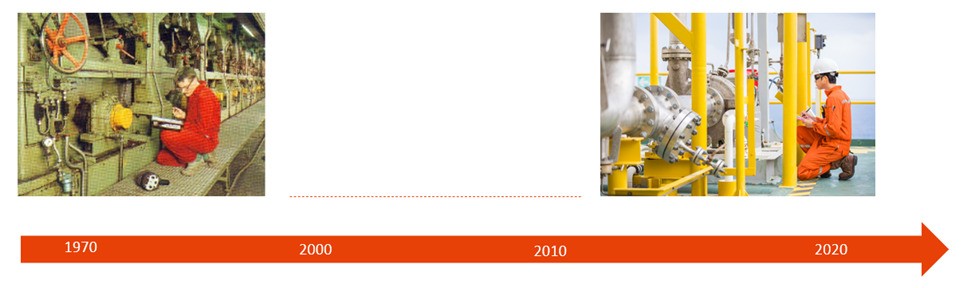
Condition monitoring was once, by necessity, a very manual role in manufacturing and process industries. You would think that as our economic, industrial and technological worlds have evolved, so too would the task of monitoring machine conditions.
Unfortunately, it hasn’t. Safety standards and industry tools have changed over time; however, the task of monitoring machine conditions has remained startlingly similar to what it might have been 50 years ago. A typical workday in the industry today closely resembles what it always has, and in that observation lies opportunity.
Machine condition monitoring is now a robust industry with solid growth prospects. Market Reports World valued the machine condition monitoring market at USD 1883.6 million in 2017 and expected it to reach USD 2551.9 million by 2023 at a compound annual growth rate (CAGR) of 5.22%, over the period of 2018 to 2023.
While condition monitoring needed to operate the way it did in the past, today, it doesn’t have to remain stagnant. There are better ways that bring critical improvements to how organisations maintain their machine assets. Although there may be deep experience and knowledge in the current workforce tasked with manual condition monitoring responsibilities, the reality is that waiting too long to evolve any job function can create inefficiencies.
Why condition monitoring now offers high-end technical employment opportunities
Condition monitoring is a knowledge-driven role now that remote monitoring is becoming more common. The discipline offers promising futures for people with technical, mathematical, and mechanical aptitude.
Advances in remote applications that demand more technical skills could improve the industrial skills gap. In addition, new grads with university degrees in mathematics, engineering, physics, or programming may find an appealing fit in manufacturing or process industry roles they may not have considered in the past.
Manufacturing and process industry organisations may now be able to hire for more roles in:
- data science
- digitalisation
- data modeling
- engineering
- data analysis
- information technology
The more sophisticated the work organisations need, the greater the likelihood they’ll hire new people to handle monitoring, data collection, and the resulting analysis. Those with practical experience and education will have great opportunities to advance within a workforce needing numbers and new energy.
Attracting the right talent necessary to industry evolution
The manufacturing workforce faces change as workers age out of roles and job responsibilities begin to shift to align with technological advances. While this can create growing pains for an organisation, it also represents an opportunity to make necessary shifts that bring other benefits to your bottom line.
Automation is the key to elevating the industry and attracting new talent. Therefore, organisations looking to recruit and hire new employees should review current condition monitoring systems. When you as a leader embrace remote condition monitoring and implement it company-wide, the types of roles you need to hire for will change. Suddenly travel and commute time can be reduced, and manual labour decreases. Jobs also become less physically taxing and more intellectually stimulating.
Over time, improvements to how companies manage condition monitoring will create room for new employees (or advancement of existing employees.) You’ll also have a chance to help people visualise careers in manufacturing and allow them to imagine a new avenue of opportunities in industry roles that have had meaningful upgrades to job descriptions and advancement potential.
Creating a culture of change
Organisations are beginning to embrace change, but movement can be slow. Leaders will need to be open to the automation and digitisation that are transforming the industry and work to attract new talent. They’ll also need to upskill their current workforce to address skills gaps.
There are still obstacles to overcome. Many organisations think cost or a lack of resources are the only barriers to improving their maintenance success. Some would identify a lack of understanding of new technologies as their main issue. However, changing organisational culture is often a key factor to embracing the future.
Increasing adoption levels of remote condition monitoring can dramatically improve how you maximise machine health. You can make significant gains in keeping production levels at optimal levels while reducing expensive downtime. In addition, these shifts will better position you to make broader changes in hiring and managing your condition monitoring.
You can encourage collaborative discussion and decision-making to ensure forward movement includes insights from all areas of your organisation. For example, with input from maintenance, engineering, purchasing, accounting, information technology and human resources, you can weigh relevant information and make better decisions about condition monitoring.
Remote condition monitoring offers manufacturing and process industries the opportunity to cut costs and decrease downtime, as well as attract a new generation of skilled technical workers. Our expert team at Condence can offer unique and customisable solutions to bring new efficiency to your remote condition monitoring while also supporting the necessary changes your organisation may be experiencing.
Are you interested in what Condence can do for you? We’d like to tell more and elaborate on various use cases. Please book a demo or send a message and we’ll explain what Condence has to offer in more detail.
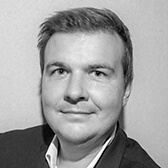
Janne-Pekka Karttunen / CEO
janne-pekka.karttunen@distence.fi
0 Comments