A manufacturing company had been experiencing issues with their production equipment, specifically with bearing failures in electric motors and fans. These had eventually resulted in costly repairs and downtime. The company had implemented a vibration-based condition monitoring program with traditional threshold monitoring to detect issues in their equipment.
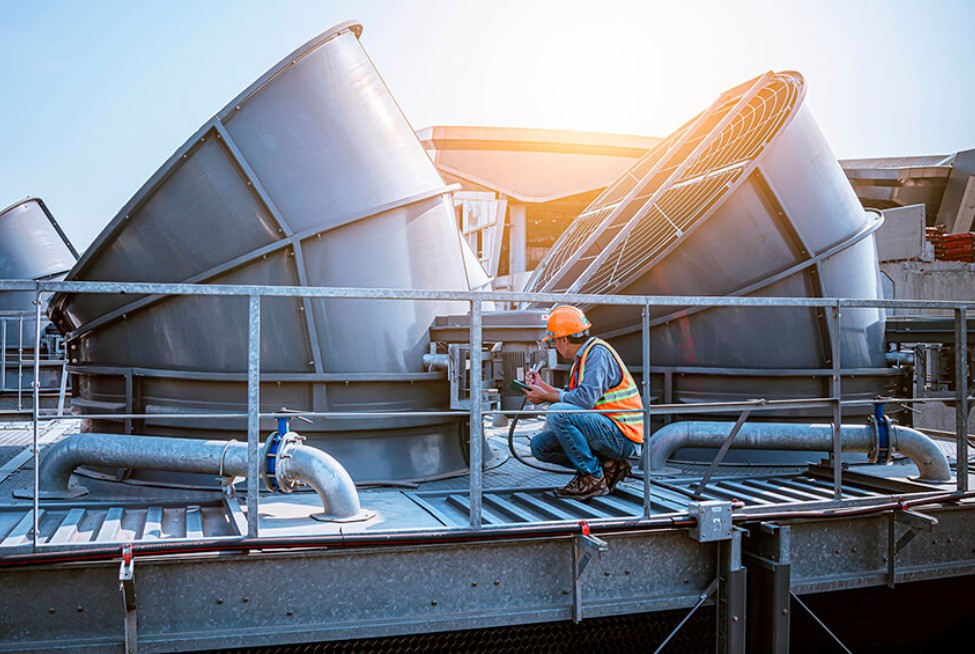
This example is built using data from a real industrial fan case that was then processed with the new digital co-engineer feature called Coe.
Problem
The customer concluded that the regular, threshold-based condition monitoring routine was not enough to improve the equipment availability. Additionally, setting the thresholds required expertise which was in short supply. In addition, operators were not fully satisfied with the results achieved.
Solution
With Coe in place to automatically monitor the continuously collected vibration samples, the customer was able to detect potential issues and anomalies that might not have been detectable early enough with traditional threshold monitoring.
Coe detected an emerging bearing failure over a year before traditional threshold monitoring would have alerted the user to the issue. The system provided actionable recommendations, enabling the company to perform maintenance before the equipment failed, saving them money and avoiding downtime.
Coe gave the first indication of problems based on its analysis and anomaly detection -386 days before an action was indicated based on traditional threshold monitoring. Mechanical issues were indicated by Coe at -235 and -122 days. Mechanical issues typically include issues such as imbalance, looseness and misalignment.
“Plan service” – recommendation was triggered by Coe -67 days before the “analyst” gave a recommendation for bearing change in real life.
Coe also provides trend visualization as evidence and additional information for operators to
evaluate.
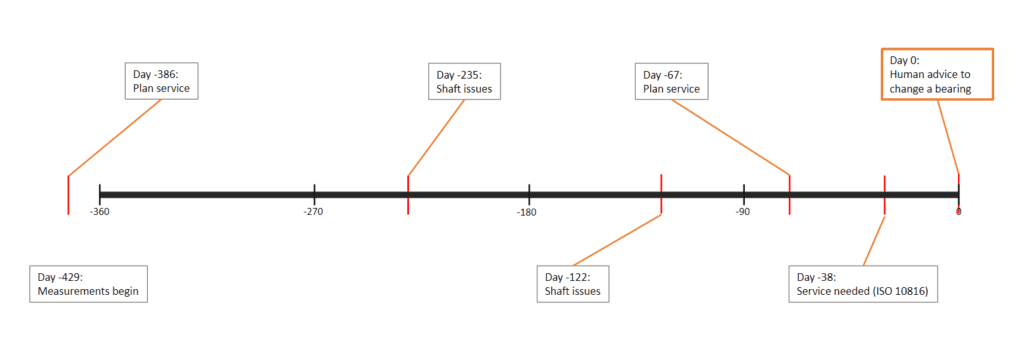
Results
Coe can give suggestions and indications on emerging issues. With these suggestions, the maintenance team can easily keep an eye on the development of symptoms and plan further actions. With automated analytics and simplified metrics, it is easy to understand where to look. Having sufficient time to detect and follow the event will allow better planning in execution of maintenance activities.
Save time and money. Maintenance planning, execution of maintenance tasks at the optimal time in relation to production needs, hours, allocation of service hours to the most critical equipment.
Book a demo to discover how Condence can revamp the way your organisation.
0 Comments