Introduction
This customer is a global forestry company operating in Finland. For them, sustainability is a key driver. That, together with work safety, made it important to introduce condition monitoring to this site. Prior to Condence, there was no online condition monitoring in place. The objective was to improve situational awareness and to increase reliability in the production, with the easiest first steps possible.
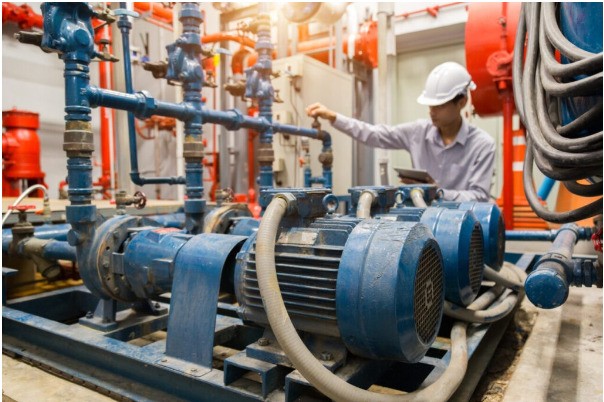
Problem
A critical processing unit on the site was fully in the blind spot for the maintenance team onsite. This processing unit belongs to the production support systems. It is important as it is responsible of all waste handling from all the production lines on the site. This processing unit is formed of a conveyor, shredder, and blower. Without proper situational awareness, undetected failures in this process unit will stop the whole production in a matter of minutes. During production, it is unsafe and impossible to perform manual measurements with any kind of hand-held equipment. The maintenance team onsite needed to have an early warning system in case this hard-to-access process unit would have an issue of any kind.
Solution
The customer chose the Condence Easy wireless deployment. It was the fastest to install to the bearing blocks and was based on a standardized measurement method (alarm levels from ISO standards). Easy sensor with its 3-axis vibration and temperature measurement provides a straightforward view of the health of the machinery. It was also important to have IP-graded sensors in the harsh and dusty operating environment.
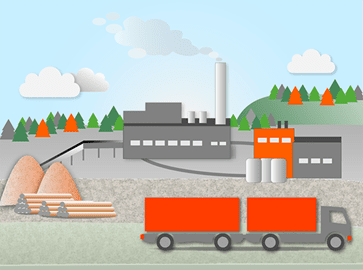
Results
The customer gained better situational awareness of the most critical process unit on the site with a fast and easy-to-install solution. The monitored machinery, waste handling unit, is custom-made and from the 60’s, so in addition to the threshold alarms, the Condence Anomaly Revealer was proven to be handy. The Anomaly Revealer investigates historical values and creates a pattern/rule of normal and suggested limits.
The team onsite was very pleased with the sensitivity of Condence. Even though the operation of the shredder is very violent, Condence could detect the tougher clumps of waste being processed. This gained situational awareness also gives the customer ability to adjust the optimal usage of the waste handling unit and have an impact on its remaining useful lifetime.
Before online condition monitoring, there was no online information available from production waste handling. The customer is satisfied that fast changes in machine health are now flagged, and temperature measurements lower the fear of overheating of bearings that otherwise would be left unnoticed. In a dusty environment, with this hard-to-access process unit, the improvement is significant.
Verifying the results of maintenance and service actions and making it easy to track the condition of the device, equips the maintenance team with more tools to plan and schedule needed maintenance actions. They are now in control and base their actions on the actual condition of the shredder unit. With successful actions, the customer can increase the reliability of the whole production process.
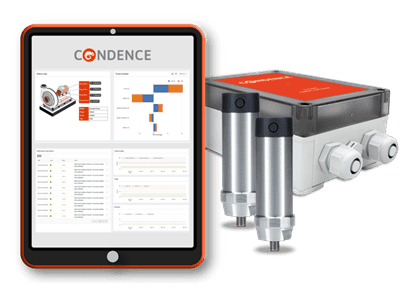
Hard to reach but easy to monitor
Condence Easy is what it’s called: the most affordable and simple monitoring option. The most optimal use is for machines that are subject to frequent manual inspection of the overall vibration level.
Monitoring options are highly standardised, and alarm levels are based on ISO-standard overall levels (consider feasibility).
Condence Easy can easily be applied to any suitable machinery.
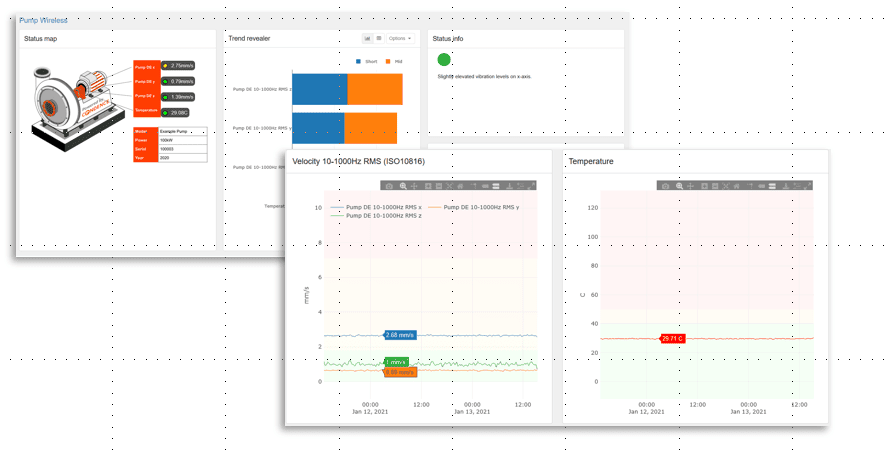
The Benefits
Wireless sensors make installation easy and straightforward. The sensors create an innovative mesh network, and one gateway can connect up to 15 sensors.
Multiple axis and temperatures will provide a simple picture of the overall vibration of the machinery that is trended in the Condence UI. In case vibration levels are elevated, an alarm is triggered.
To visualise and analyse the development of measurements, Condence provides a standard view.
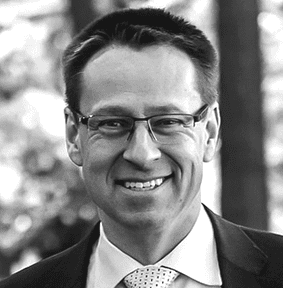
Timo Tammisto
Member of the board and CEO and Partner at Miston Oy.
Timo has several years of experience with both small and large public IT- and consulting companies in the US. He served as the CEO of the technical trading company Solotop for ten years.
0 Comments