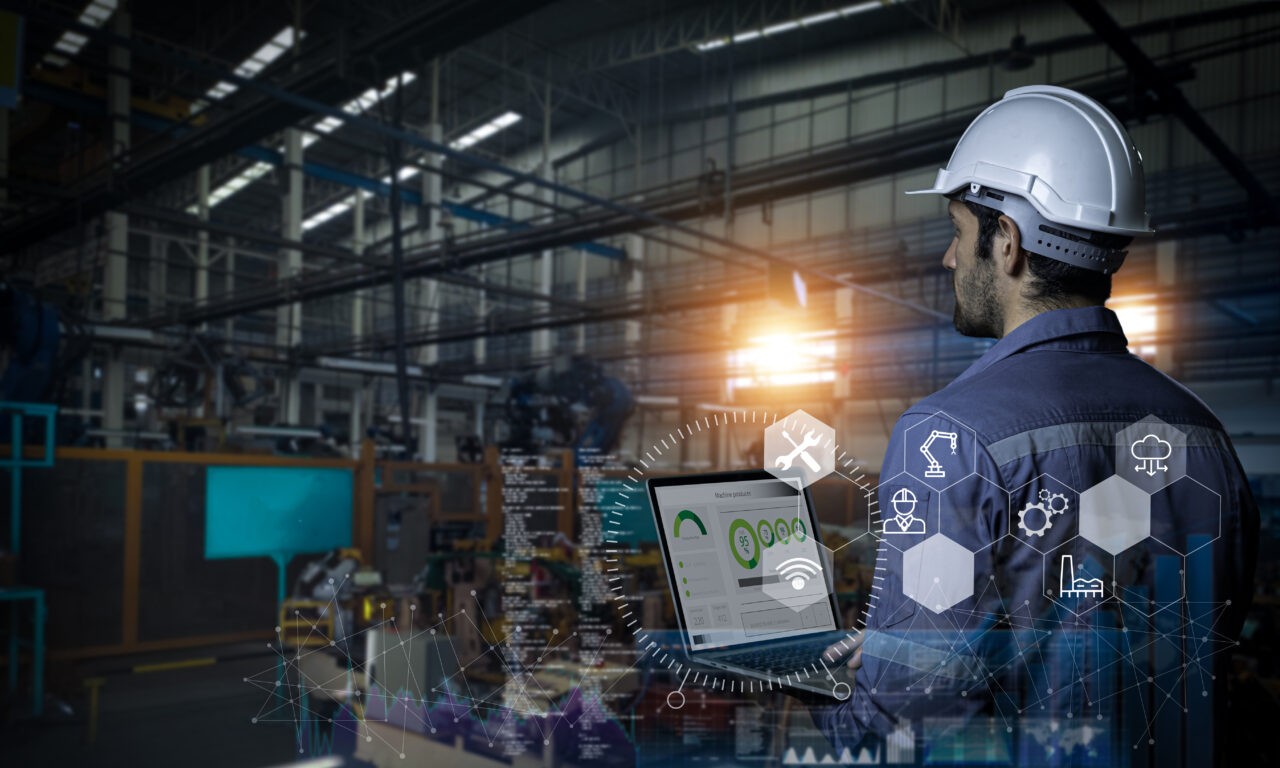
Sustainable Leadership in Digitizing Condition Monitoring
By Timo Tammisto – October 2022
The early movers in this field have a lot to gain. Not only do they fortify the customer
relationship, but the owner of the platform stands in the middle of it all as the gatekeeper for all interaction and data flow.
During the pandemic, the movement of people was severely restricted, at times both locally and for extended periods across borders. Yet, while some industries, like the HoReCa sector, came to a near-total halt, other industries had to keep on running. We still need energy, heat, water, and goods to consume, in other words, manufacturing. That meant a lot of rotating machines, pumps, motors, gears, turbines, fans had to keep on running and guarantee the necessities we so depend on remained available.
Travel restrictions coupled with the globalized nature of our economy resulted in some seriously hairy days for the maintenance and service sector and those responsible for the reliability of processes. Physical access to plants was a nightmare. This was a serious wake-up call for many. How much do we rely on physical presence and manual tasks? How can we learn from these few years and mitigate this dependency? This wake-up call, combined with the long-brewing notion that maintenance and service operations have been falling way behind in digitalization, gave a boost for those ready to seize the opportunity and look further out.
In the IT industry, the remote control has been a norm for years. No need to physically go and work on someone’s laptop or server; a remote connection to diagnose and often to solve an issue is enough. Fast, efficient, and economical. Again, during the pandemic, solutions to connect people emerged, such as Zoom, Teams and Meet. But what about connecting machines, especially mechanical, such as the rotating machines that have next to no intelligence? These machines are the bread and butter for maintenance and service organizations. They are often critical, run constantly and have plenty of wearing parts. They need constant monitoring; a small budding issue develops insidiously into a full failure.
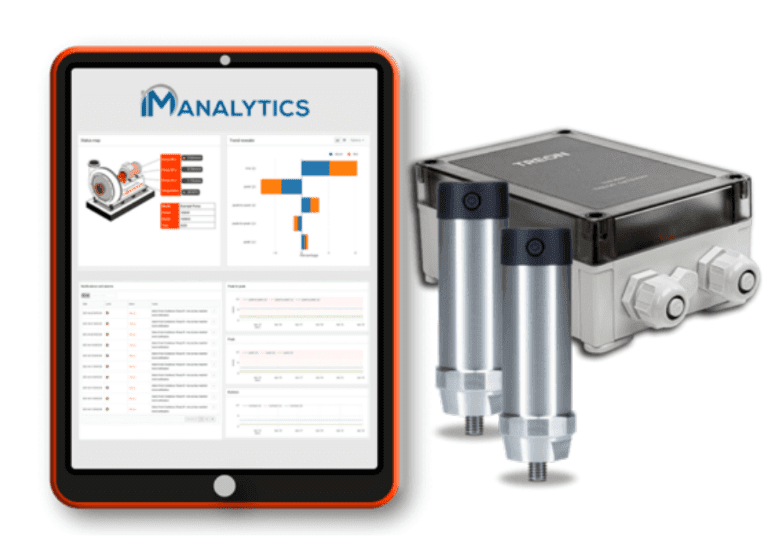
Many companies came to the realization during the pandemic that we can do better. The good news is that the technology to build the Zooms and Teams for industrial assets is and has been here for quite some time. It is mature and ready to scale fast. Today, advanced PdM systems (Predictive Maintenance) deliver significant advantages, and those who have adopted them are increasing their lead to the followers. (See McKinsey, 2021: A smarter way to digitize maintenance and reliability¹) One successful example of this is the IMAnalytics solution being rolled out by the Power Transmission Solutions group of Axel Johnson International. A group-level advanced industrial maintenance analytics solution developed to execute the strategic digitalization initiative within the organization.
To better understand a condition monitoring platform, let’s take a closer look at the example. The IMAnalytics solution is built with the mindset that every rotating machine can be monitored. It is based on condence.io technology from Distence Ltd and comes with 15 years of research and experience from demanding industrial settings. The solution itself comprises of three parts. The cloud-based IMAnalytics platform is for data collection, sharing, and analysis. It transforms the data from remote assets into actionable information, visualizations, and forecasts. It can track countless assets and sort out the ones that need attention regardless of their type or physical location. The remote monitoring electronics on the field process the data from various sensors and transfers it intelligently to the platform. The third part is made up of the various sensors used to gather data from any given asset, such as vibration, oil quality and temperature sensors. Naturally, you can collect any related data from an asset to complement condition data with the same system. In rotating machines, the anomalies detected can include, for example, analysis of vibrations, lubrication related issues, bearing failures, overheating, and misalignment.
Case IMAnalytics
The system can be used flexibly to support field crews to monitor remote assets such as pump stations or fans in tunnels. It can just as well be used to increase reliability in a factory setting, helping assure any given asset is performing and not giving surprises. Advanced tools on the platform help professionals analyze data. Various anomaly detection and visualization tools help service organizations understand events in the history of an asset and predict future ones. It digitizes the life of an asset and helps operations and maintenance organizations plan better, avoid surprises, and ultimately increase the assets and the underlying process’s reliability radically.
Critical for the Power Transmission Solutions group of Axel Johnson International was how the Distence business- and partner model with the condence.io solution fits into their strategic initiative of digitalization. How the model supports the way the operations are built, what the offering is as a whole and how flexible it is.
Above and beyond detecting faulty assets
It is beneficial to acknowledge early on that even though remote monitoring as such is enough reason to invest in the technology, the value goes far beyond just capturing a failing component. The efficiencies of running a service and maintenance organization based on real-time data go far beyond the daily maintenance operations. The value of the information generated by the PdM system for other stakeholders in the organization say sales and logistics, and the gains in sustainability are just a few dimensions worth considering. When viewed at a group level, the direct savings, efficiencies, eliminated kilometres and hours of needless driving, and optimized spare parts inventories add up to enormous savings and boost both employee satisfaction and safety on the field. “Unplanned downtime costs industrial manufacturers an estimated $50 billion USD each year, according to Deloitte. Machine condition monitoring, when done effectively, has the potential to increase efficiency, reduce expensive downtime, and boost productivity in manufacturing.”, writes Panu Kinnari in his article “The industry bias against online condition monitoring”2.
As is the case in many business ventures, early adopters take the lead. But in the case of digitizing condition monitoring, the early adopters can not only take the lead but can secure it for years to come for the advantage of the supplier, the customer, and the employees.
Already back in 2014 M. Porter and J. Heppelmann wrote in their article titled How Smart Connected Products Are Transforming Competition3 about how information technology is revolutionizing products, the benefits of connected products and the evolution of products into a system-of-systems ecosystem. When embarking on this journey, there are some critical strategic decisions a company must make regarding business models, technology architecture, and partnerships. Their conclusion highlights how this drives innovation and economic growth. Today we are already far on this journey.
It is natural that digitalization starts from where it is the easiest, products that already have the capability to be connected or have some level of IT embedded in them. Mechanical machines, though extremely critical for any process, have been followers. The past few years have finally given them their time in the spotlight.
The maturity of the technology enables organizations, like is the case with Axel Johnson International and their IMAnalytics, to roll out their digitalization strategies into service and maintenance operations without having to think if the system itself works. The technology exists and is proven. The focus can be on strategy. New business models are now up to the imagination of the business leaders, such as compressed air or engines for airplanes as a service. The expertise or service engineers can be directed to where it matters and adds value, not on remedial or supporting tasks. The enormous amount of money tied up in spare parts and the time tied up in logistics can be radically enhanced with data-driven operations. No need to drive to check on an asset; just log in to your PdM system. The opportunities are endless.
The Drivers for Change
The drivers for digitizing the condition monitoring of industrial assets touch all aspects of business management and strategy. The more critical for this context include areas such as:
People – give professionals the opportunity to develop
In any maintenance organization, professional people are in the center of operations. They are the ones who go on-site, analyze, decide on the required action, do the actual work and finally the paperwork. They are the lonely soldiers in the trenches. Most of us in the industry can name individuals in our organizations, the ones to call on when there is a critical issue. And the ones the colleagues call when they are challenged.
The world has changed, however. Before digitalization, information remained very much in the head, or at best on the laptop, of the service engineer. This system, focused on the individual, is both vulnerable and hinders information sharing, learning and continuity. Technology can now assist and let the service engineers focus on where their professional training comes in best use. A daily and very concrete example of this is service visits. It is not motivating or financially viable for two engineers to drive to a remote location to check on a pump. Something you can check and monitor online at a fraction of the cost.
The transition to using digital tools can be scary, some might take it as a threat to job security or simply it’s the natural human tendency to resist change. But it is the exact opposite. The tools reduce paperwork, the unmotivating repetitive tasks, and the hours and hours on the road. The tools, as will be later discussed, help bring more value, faster and at the correct time to the customer, resulting in higher customer satisfaction and less stress to the engineer. They increase the intellectual aspect of the job and allow more of the time to be used for value-add tasks. Less crisis and more planning.
Naturally, the transition needs to be managed. Dumping a PdM system on any organization is both unfair and poor change management. Training is key, as is a gradual adoption of the new system. Highly productized systems, such as the IMAnalytics, are fast to install and easy to pilot. Start small, prove the value and transition to the new model gradually but decisively. An internal sponsor and a goal-oriented mind is important. The last thing you want is for the limbic system to trigger a freeze in the face of new technology, a Kodak moment, missing on a technology radically shaking the industry.
Information – Data gives us insight to be better
Digitalization facilitates not only the transfer, sharing and analysis of the data but also the combining and correlating. Instead of sporadic handheld metering, statistically valid continuous feed of the most critical vital signs of a machine is delivered to your dashboard and analyzed with suggested actions at a fraction of the cost of manual visits in person. Total transparency to the assets’ life. Easily adaptable to whatever is critical for each asset, be it vibration, temperature, quality of lubrication and combining it with environmental or operational data. At best, build a visualization of who is using the asset, where and in what environment it is located, how it is performing, how it is being used and what condition it is in? All this with a time dimension. Immediate feedback from the machine versus a visit from the field crew. The full life of an asset at your desktop. Combined with the expertise of the service engineers, it gives the organization a strong competitive edge.
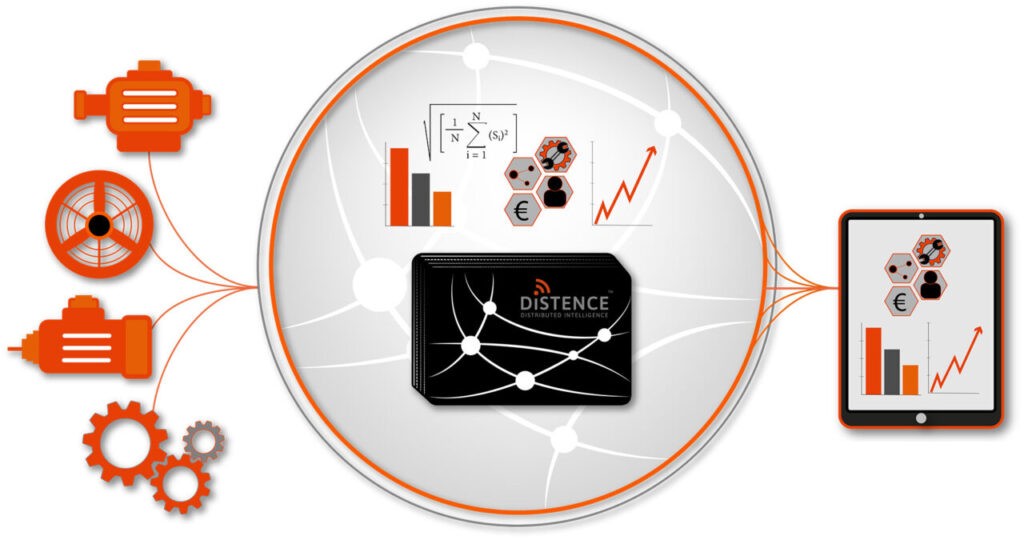
The technology capturing the data is only one aspect of the equation. The platform that collects and analyses the data and translates it to actionable information is where the magic happens. In the Harvard Business Review: Pipelines, Platforms, and the New Rules of Strategy4, authors discuss various platforms, their evolution and above all, the move from Pipelines to Platforms. Though the examples are more from the consumer world, a lot of the same underlying principles apply here. The chief assets are information and interaction, they write.
It is critical that the connection with the asset does not remain a one-to-one pipeline but evolves into a many-to-many platform for information and interaction and is integrated into other systems. The information produced cannot remain in the hands of a maintenance engineer but should be shared with sales, R&D, financials, logistics and whoever can benefit from it. R&D can design better products, sales can get a head start on selling new machines to replace dying ones, financial people learn about total cost of ownership (TCO) and profitability of operations and maintenance, and logistics learn what spare parts to hold in stock and where. Information is valuable, it helps promote expertise and bring more value to the customer relationship.
However, there is no need to do everything at once. The daily operations of the service and maintenance organization is a good place to start. One asset group at a time. The platform is ready to expand and share when the organization is ready to benefit from it.
Money – profitable business safeguards continuity
The key driver to most investments is money. The quest for more sales and profitability. Remote predictive condition monitoring serves as an excellent tool to achieve exactly this. In two earlier articles, I dig deeper into the opportunities. (“Increasing the Return on Investment – a holistic view on benefits from digitalization”5 and “Why should CFOs in industrial companies be all over edge computing?”6) Here is a synopsis of some of the opportunities.
The ROI from digitalization comes from both cost savings and from increased revenues, both in the form of customer retention as well as new business. The cost of remote monitoring runs in some tens of euros per month per asset. At that cost, and when compared to the cost of labour hours, the financial calculations in the benefit of remote monitoring are easy to do.
On the revenue side, in addition to transactional costs, building monthly recurring revenue streams (MRR) is one of the bigger opportunities. New business models are emerging and challenging the old.
Time to service is critical. What spare parts should we have at hand, and where? In the process industry, what assets should be serviced or replaced during the scheduled service stoppage? Are we reactive or using continuous analysis of information and planning accordingly? A crisis is almost always costly, but with planning, we can optimize.
As a summary from the above-mentioned articles on the financials, here are some key areas for opportunities to consider:
1. Transparency. Establishing a 24/7 “umbilical cord” to assets. A source of information to facilitate design and innovation both in technology and business modelling.
2. Continuous Improvement. Through direct access to the assets, how they perform and how they are being used, continuous adjustments are possible.
3. Asset Management. Managing and extending the life cycle of each asset. Knowing what you own and what shape it is in.
4. Utilization. Optimizing the performance and uptime of assets.
5. Maintenance. Enabling the evolution from reactive to preventive to predictive maintenance. Reducing direct labour, driving times of mobile crews, simplifying logistics, knowing what spare parts are needed etc.
6. Safety and Training. By learning from how the machines are used, serviced and handled, the operator can benefit from focusing the training on the relevant areas in order to increase productivity, safety and the life span of the machines.
7. Performance. Thanks to continuous and comparable data – relevant key performance indicators can be built for each asset and process.
8. Modernization. Turning “dumb” machines into intelligent by retrofitting them with intelligent devices.
9. Customer-centric design. By understanding how the asset is really used in the customers environment, the R&D organization can better design products from the customer perspective.
10. Data availability. Today the data is trapped in the heads of the service engineers or their laptops. Modern tools and the architectures they are built with make data available for everyone in the organization to benefit from, from O&M to sales to finance.
11. Sustainability and Circularity. Understand and cut the carbon footprint, emissions, energy use and life of an asset.
Customers – our customers are our partners
Is there anything more important in business than your customer relationship? The most expensive customer is the one who you have been chasing and marketing to but who buys only once. Repeat customers and those we do ongoing business with are the keepers. Both benefit from the mutual knowledge of each other and trust. This requires interaction and information. The most successful and long-lasting businesses do anything and everything to build and keep their customers. Customer loyalty comes from mutual respect and the competitive value-add offered to the customer. Remote condition monitoring offers the tools to build this customer intimacy. The ability to predict problems, avoid unplanned shutdowns, offer information and expertise, and provide suggestions for improvement – all would be virtually impossible without information. Digitalization offers the tools to build resilience into the relationship and take customer service and retention to the next level.
Sustainability – holy cow, the amount of waste that we create
Condition monitoring touches on sustainability from numerous angles. The way we work today, driving endless kilometres to check on an asset, driving back to get a spare part and back again to fix it, simply does not make sense anymore. Not when there are tools to detect even the most budding of anomalies, track their development, identify the failing component, and optimize the time to service. Even if you can eliminate a fraction of those kilometres, nature says, Thank You! And that is just the operations side of things.
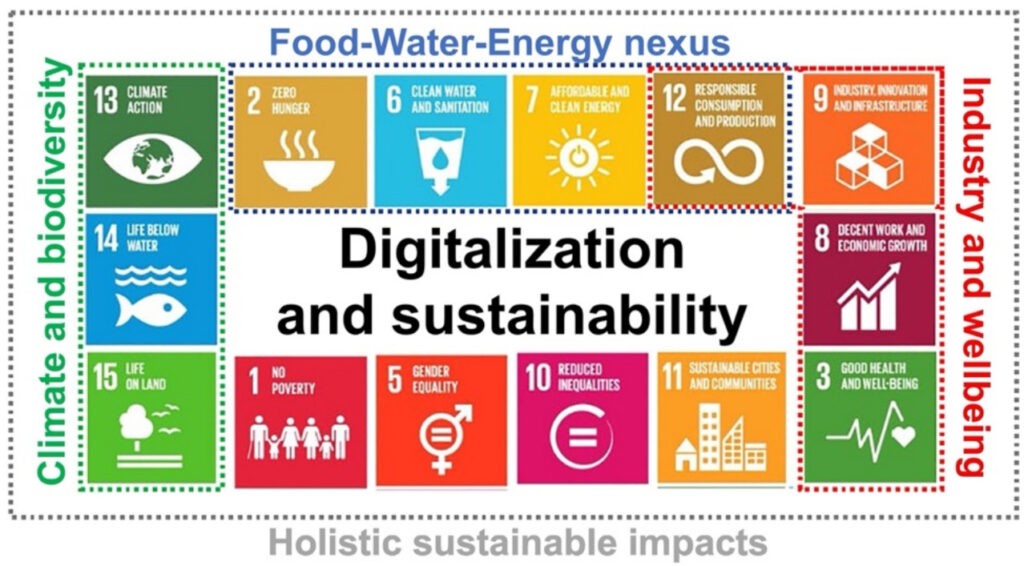
Optimizing asset usage, understanding how and when they are used, combining information from frequency converters with asset data, optimizing for energy consumption and above all, extending the life of millions of assets opens a huge opportunity to contribute towards sustainability.
Erik Mosselaar, in his article: “Condition monitoring: driving progress toward sustainability goals”, ⁷ outlines seven ways manufacturers can impact sustainability goals:
1. Power consumption
2. Carbon dioxide emissions
3. Industrial Pumps
4. Using refurbished versus new components
5. Maintenance and resource management
6. Turn consumables like industrial oil into assets
7. Cutting production waste
From the above list, Industrial Pumps is singled out as an asset group because of their abundance and market size. It represents annually a global market of some 60-90 billion USD and growing steadily. That’s a lot of pumps. Running continuously, the bearings wear out, significantly increasing energy consumption and reducing efficiency. Multiplied by the sheer numbers, the impact on sustainability goals is one of the biggest opportunities to make an impact.
Sustainability is among the biggest winners when investing in remote condition monitoring solutions.
Conclusion
There is no successful organization in the world that does not think about cost savings, new revenue streams, and happy customers and employees. The Service and Maintenance -field can benefit radically from digitalization, something that so many other industries have already built as a standard into their operations.
The modern technological innovations in this field and the maturity of both the platforms and the measurement technologies support digitalization and the adoption of new processes. The competitive advantage comes to those who can offer their customers the best expertise and service at a competitive cost. That is a combination of data-driven operations and modern processes together with the people in the organization. Being able to give insights is what delights the customer – an advanced PdM offers exactly that. For the people working in this area, it offers safety on the job, more satisfying work and converting emergencies to planned operations, just to name a few benefits.
Digitizing industrial remote condition monitoring opens huge opportunities to those ready to rethink and modernize the industry that supports many of the critical processes in our society. It gives us a tool to help us and our customers do our part for sustainability and circularity.
References and further reading
1McKinsey, 2021: A smarter way to digitize maintenance and reliability. https://www.mckinsey.com/business-functions/operations/our-insights/a-smarter-way-to digitize-maintenance-and-reliability
2https://condence.io/2022/08/19/the-industry-bias-against-online-condition-monitoring/
3Harvard Business Review: How Smart Connected Products Are Transforming Competition by Michael E. Porter and James E. Heppelmann.
4Harvard Business Review: Pipelines, Platforms, and the New Rules of Strategy. By Marshall W. Van Alstyne, Geoffrey G. Parker, and Sangeet Paul Choudary.
5https://www.linkedin.com/pulse/part-2-increasing-return-investment-holistic-view-from timo-tammisto/
6https://www.linkedin.com/pulse/why-should-cfos-industrial-companies-all-over-edge timo-tammisto/
7https://condence.io/2022/06/01/condition-monitoring-driving-progress-toward sustainability-goals/
IMAnalytics by Power Transmission Solutions group of Axel Johnson International
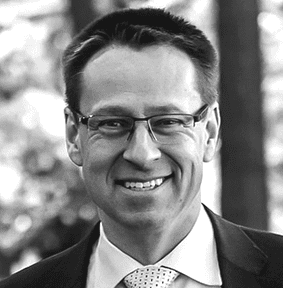
Timo Tammisto
Member of the board and CEO and Partner at Miston Oy.
Timo has several years of experience with both small and large public IT- and consulting companies in the US. He served as the CEO of the technical trading company Solotop for ten years.
0 Comments