Proper lubrication is one key element in keeping rotating machinery healthy and in operation. Many on-line and IIoT systems claim to provide an ideal solution for lubrication. What does this mean? Where does this fit in? How should it be used? We believe that a one-size-fits-all approach does not apply. We will try to explain how we circumvent biases like this with Condence.io. We offer multiple methods and combinations of them, depending on need, feasibility, and desired results or objectives.
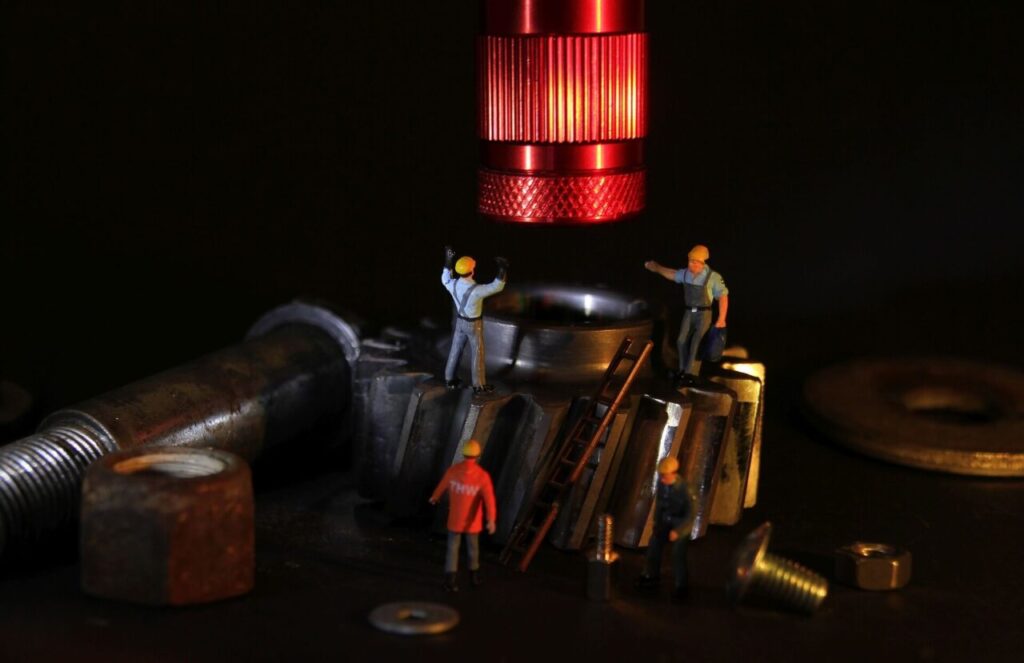
Detecting the presence of friction
Let’s start with the primitive methods where detection of improper lubrication is one of the objectives. Traditional methods like temperature or wideband noise in vibration can indicate lubrication issues. As said, these are common, however primitive, and detect issues at a relatively late stage. Therefore, many asset owners turn to more specialized methods, like ultrasound.
One emerging method to detecting such issues, especially with fluid film bearings, is the measurement of mechanical stress with a Force Detection Sensor (FDS). Based on our experience this is a great alternative to proximity probes, especially for retrofit situations. This technology is something to follow and we have multiple cases on track around this, to be published soon.
Alternatively, Condence.io has introduced a signal processing method with a standard vibration sensor to detect phenomena commonly observed only with ultrasonics. A sample acquired with a common high fMax 10kHz accelerometer can expose friction. Measuring the present friction is highly beneficial if one is trying to figure out an accurate greasing routine or simply wants to confirm a successfully performed task.
Detecting the progress of wear or contamination
Oil and lubrication analysis can also be a powerful tool in preventive maintenance. For example, deriving wear and tear from detecting and calculating metallic particles. In certain situations, like slowly rotating bearings, developing cage issues are only seldomly observable in lab samples. In many cases when it is detected, the issue has already progressed far. And, as is the case with water leakage, the wear process starts within hours after water reaches the oil, so we are likely to see the symptom and not the root cause. This is simply to note that we need to understand the limitations of various methods.
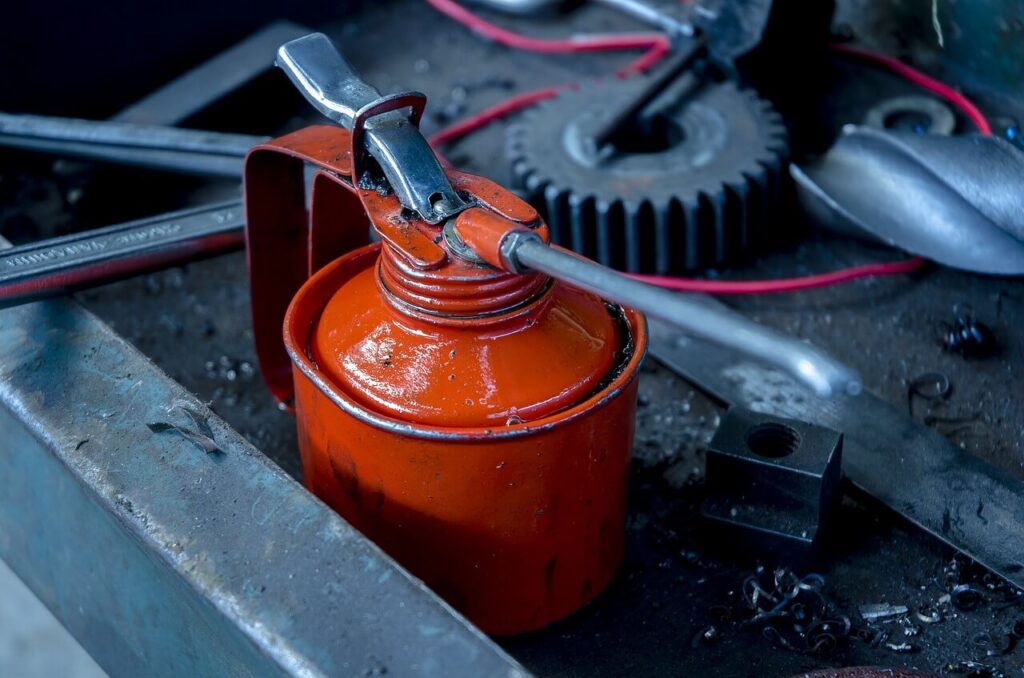
When the lubrication system is a part of a large and complex installation, monitoring oil and lubricants is also is also a very efficient way to keep track of potential wear and tear. There are compelling reasons to monitor particles; Condence.io analyses and provides cumulative particle trending per hour and indicates particle sizes and whether these are ferrous or non-ferrous to evaluate ongoing situations.
When talking about non-ferrous particles there are many types of sources, for example an eroding seal that might contaminate the oil. Oil contamination can have many root causes by default. Some use cases that are sensitive like turbines or hydraulic systems tend to demand contamination monitoring. Condence provides sensor agnostic solutions for different applications as there are sophisticated needs.
Then there are other applications, in mining for example, where particles are being introduced to the lubrication system resulting from the production process. This leads to situations where particle counting is not always the right method. There, Condence.io offers oil color analysis to bring insights into the lubrication’s health status.
Ensuring proper condition of lubricants
Taking physical oil/grease samples has been the traditional way of ensuring the condition of a machine. There are three motivating drivers to change: 1) Sampling intervals are often long, and late detection might cause collateral damages 2) A solid manual greasing routine still is no guarantee the lubricant reaches all the right places 3) This manual process does not build up any systematic data to learn from, e.g., how to avoid potential issues on similar devices. Worth to mention of course that lab samples are often more precise and will perhaps never become obsolete. However, by adding an on-line system, improved timing is often achieved as mean time failures are common.
Manual sampling often holds monthly to multiple-month intervals. This might lead to mean time failure. As mentioned, some issues for example in water-cooled systems, might lead to significant collateral damage if detected after several days or weeks.
Implementing on-line oil quality monitoring with a chemical sensor monitoring the lubricant fitness will help with early detection of issues related to water or electric constant, temperature, pressure, etc. that might indicate severe issues in the lubrication system. Chemical sensors can also detect more slowly developing issues related to the ageing of oil.
With Condence.io we are experienced in all the above. We look beyond the monitoring to build prognostic tools and models that calculate the Remaining Useful Life Estimation (RUL) to optimize the lifecycle and condition of the oil.
Presence of varnish is one of the issues for us to address next. Detection of Varnish via the color of the oil is one of the standardized methods (ASTM D 1500). There are methods to automatize this with an on-line system. However, at an earlier stage, oxidation, which triggers varnish forming, can be prevented by timely detecting water in the oil with the help of chemical sensors. And, earlier still, one of the ways to prevent moisture from entering the system is to automatically track the proper working of desiccant breathers.
Integration and lubrication systems
A point we have not yet touched is the integration with other systems. Routines and documentation or reports are commonly collected in the CMMS. Integrating Condence.io with the CMMS is a must. In a majority of the cases, a demand for a company-wide solution integration with larger data storage, and with a system where daily routines are managed is a key driver to implement a modern condition management system.
Returning to lubrication, automated lubrication systems are becoming more popular. These systems often come with local self-diagnostics, and this is one application for an on-line system like Condence.io to automize. A typical example is an empty grease container, yet other issues that require monitoring occur as well.
Another use case to monitor and adjust proper grease routines with automated greasing systems is to detect the presence of friction. If for example a lubrication system is tuned for a bearing that also has a friction indicator applied this will detect if an adjustment or other type of attention is needed. Additionally, the system notifications can be set up in the CMMS to trigger the lubrication pods. Although Condence.io does not control processes, there is nothing to stop the user from setting this up on their end.
Conclusion
Ensuring proper lubrication is not a simple task. Lubrication is one key element of maximizing machine health and is sometimes undervalued.
With proper implementation of selected-for-purpose technology, this task can be simplified and made effective. However, this will require a flexible and knowledgeable technology partner.
Condence.io is delivered by a team with 15+ years of technical solutions experience. We have learned and continue to learn from the best minds in the market and the knowledge behind the Condence.io solutions is unmeasurable in numbers.
Would you like to add something? Do you want to donate your expertise and be an advisor? Would you like to become a value-add partner? Wish to disagree? Please comment and reach out to the author!
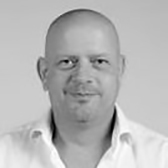
Erik Mosselaar
Sales & Business Development Manager
erik.mosselaar@distence.fi
0 Comments