In this case, the customers industrial gearboxes were manually monitored as part of their normal maintenance program. This process was, however, time-consuming, hard to scale, and costly. The customer was looking for a more efficient and effective solution.

This example is built using data from a real gearbox case that was then processed with the new digital co-engineer feature called Coe.
Problem
The manual monitoring process was not enough to detect emerging issues in the gearbox. Developing faults had too much time to develop into expensive and potentially process halting issues. In addition, manual monitoring tied up resources and lacked continuity, resulting in missed symptoms. The user was looking for a more efficient and effective solution that would help them detect and follow emerging symptoms and plan accordingly.
Solution
The customer implemented Coe. This new tool analyses vibration data from sensors installed on industrial equipment and offers suggestions and a direct link to the underlying data for a deeper look when necessary. The system automatically detects patterns or anomalies that indicate potential issues or failures and prompts the user to take action, either by sending an alert or suggesting a specific maintenance or repair task.
Coe detected the first indications of an emerging gear wheel issue approximately a year before the user deemed that further action was required. Coe provided recommendations for maintenance well in advance, enabling the company to address the issue before it led to equipment failure and downtime.
Coe gave the first indication of problems based on its analysis and anomaly detection not long after the measurements began. Suggestion at -314 days before human observation was about possible metal-metal contact or issue with lubrication and followed by a suggestion to evaluate the condition of the gears or bearing condition at -266 days.
Issues were detected and highlighted by Coe multiple times. Suggestions indicated friction as well as typical gear issues, eventually leading to costly service that could have been avoided.
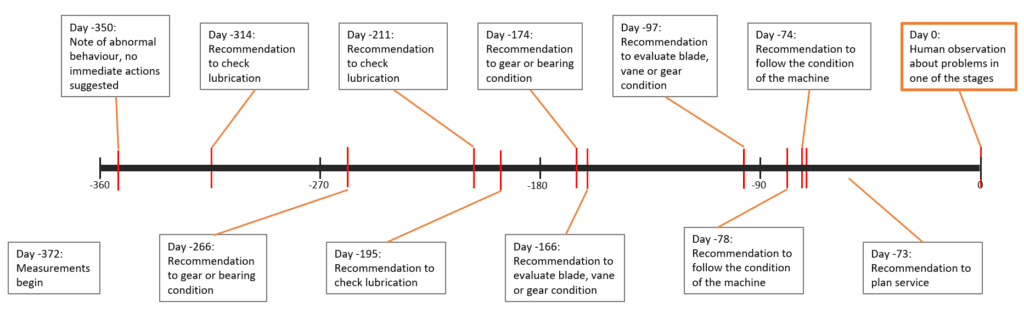
Results
By using Coe, the company would have been able to save time and reduce costs associated with equipment repairs and downtime. They would also have been able to increase their overall operational efficiency by identifying potential issues and addressing them proactively and by freeing up resources from manual inspections. Coe’s ability to learn and adapt over time means that maintenance professionals can improve their equipment maintenance strategies, enabling them to make more informed decisions about maintenance tasks and scheduling.
Book a demo to discover how Condence can revamp the way your organisation approaches maintenance.
0 Comments