Introduction
Customer with an industrial production plant working 24/7—critical process equipment in a critical part of the process. The device had four bearings in total in two bearing blocks. If any of these bearings have a failure, it will require a shutdown of the whole production line leading to significant production losses. Condence predictive condition monitoring was installed. There haven´t been any issues detected prior to taking online condition monitoring into usage.
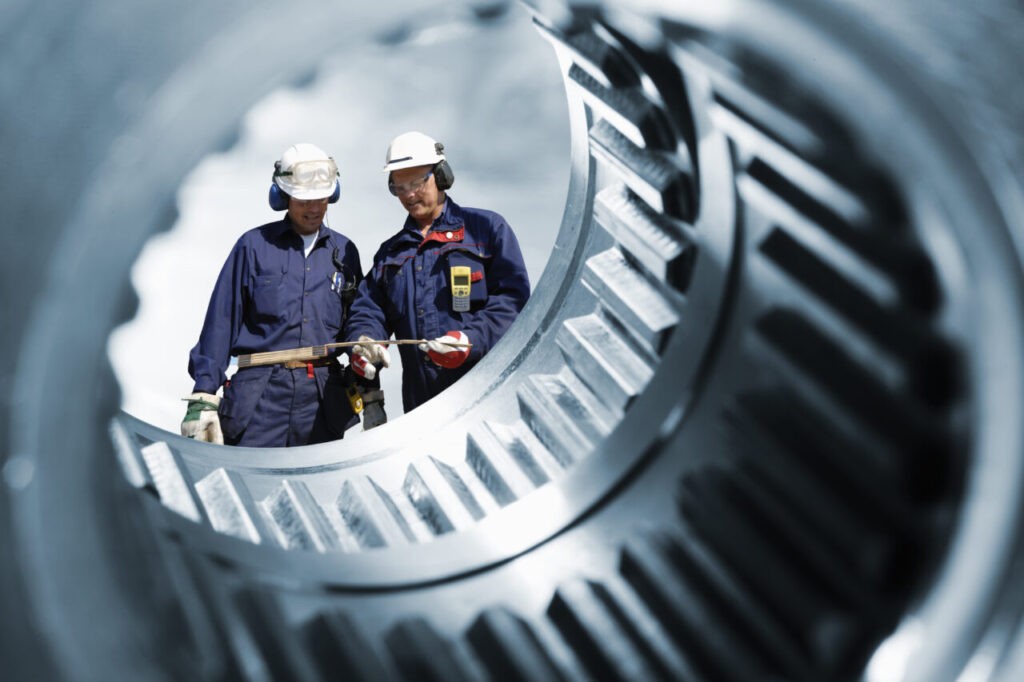
Problem
Right after the installation of Condence, it was found from the Lubrication Indicator -tool that one of the four bearings showed higher values than the rest. After two months of production, this specific bearing’s Lubrication Indicator value started to incline more rapidly. The customer added more lubricant and observed the results from Condence: Lubrication Indicator still showed too high values. The customer could see the normal levels that this bearing should have had by comparing it to a similar reference bearing. The minimum time to fix the bearing, as expensive emergency work, would have taken days. Prior to this observation, there were no plans to change the bearing in the next annual maintenance stoppage. In retrospect, the bearing had been changed in the past without updating the bearing information, making the traditional bearing detection insufficient.
The graph below shows Lubrication Indicator and how subtle the change is to catch manually with human-eye.
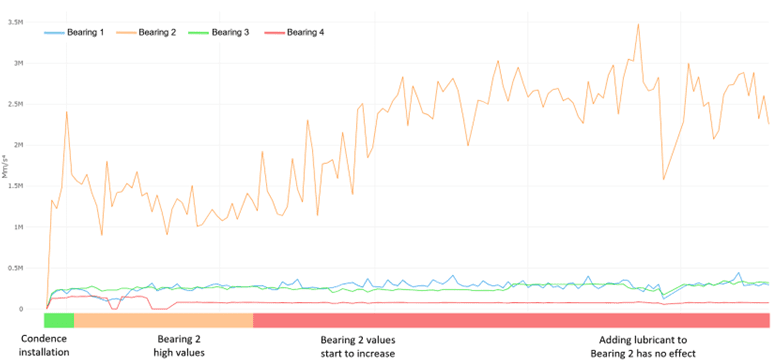
Solution
Condence Lubrication Indicator exposes friction which can be a symptom of improper lubrication or minor damage in the bearing. In case the lubrication only helps momentarily, this might be a sign of early-stage bearing failure.
It took only two months to see a notable increase in Envelope analysis after Lubrication Indicator detected a possible issue. The failure frequency trend had also started to increase, same time as the values in Lubrication Indicator, but without reaching the alarm levels. The annual maintenance stoppage was just around the corner, so the customer decided to change the bearing.
Results
In Condence Advanced level monitoring concept, one of the automatic metrics followed is Lubrication Indicator. The bearing seemed to have still a lifetime left, but with a closer look, there was an early-stage bearing failure on the outer ring. When this production equipment would have broken down, it would have led to significant costs, including repair costs and personnel costs, not to mention production losses. The customer decided to expand Condence installation in production because they were satisfied with the control they gained over the machine’s health and capability to observe lubrication conditions. With Condence, customer could fix the bearing when it was the most convenient time for them and with the minimum maintenance cost. Verifying the results of actions and making it easy to track the condition of the device in the future makes it straightforward to schedule needed maintenance actions based on the actual condition of the bearing.
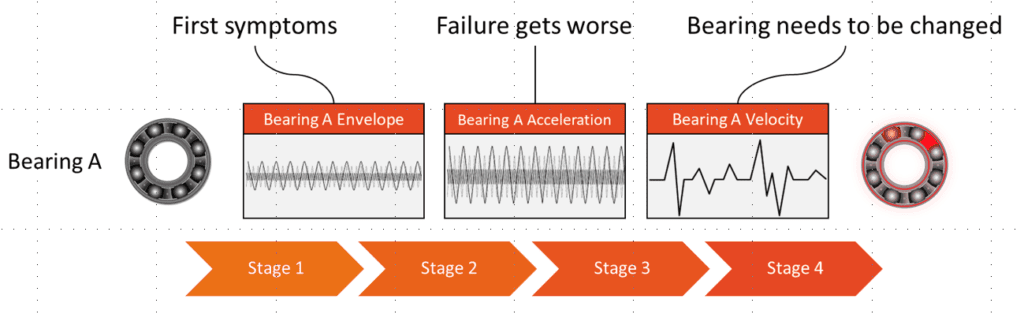
Hard to reach but easy to monitor
The most commonly used method is observing vibration, which can change in frequency or intensity as parts degrade or approach failure.
Condence Lubrication Indicator helps keep track of the lubrication status. It measures friction to determine how many devices have been lubricated and tracks if there is too little or too much lubrication. Using IEPE sensing technology to capture high-frequency vibration. Wide frequency bandwidth translates into time, time to react. Condence edge computing capability captures the earliest possible symptoms of bearing failure by enveloping acceleration. Failure stages 1-4
The Benefits
The most important goal is uninterrupted operations. Condense enables this by offering, in a very cost-efficient way, a real-time view of the assets and their health and the confidence that as the situation changes, the team has eyes on the problem and tools to analyse and track the progress of the issue.
Vibration analysis and interpretation tools serve decision-making without having to visit the site, which saves time, notably increases the efficient use of resources and allows professionals to use their time on more productive tasks than logistics and manual measurements.
0 Comments