Condition Monitoring at
Hydropower Stations
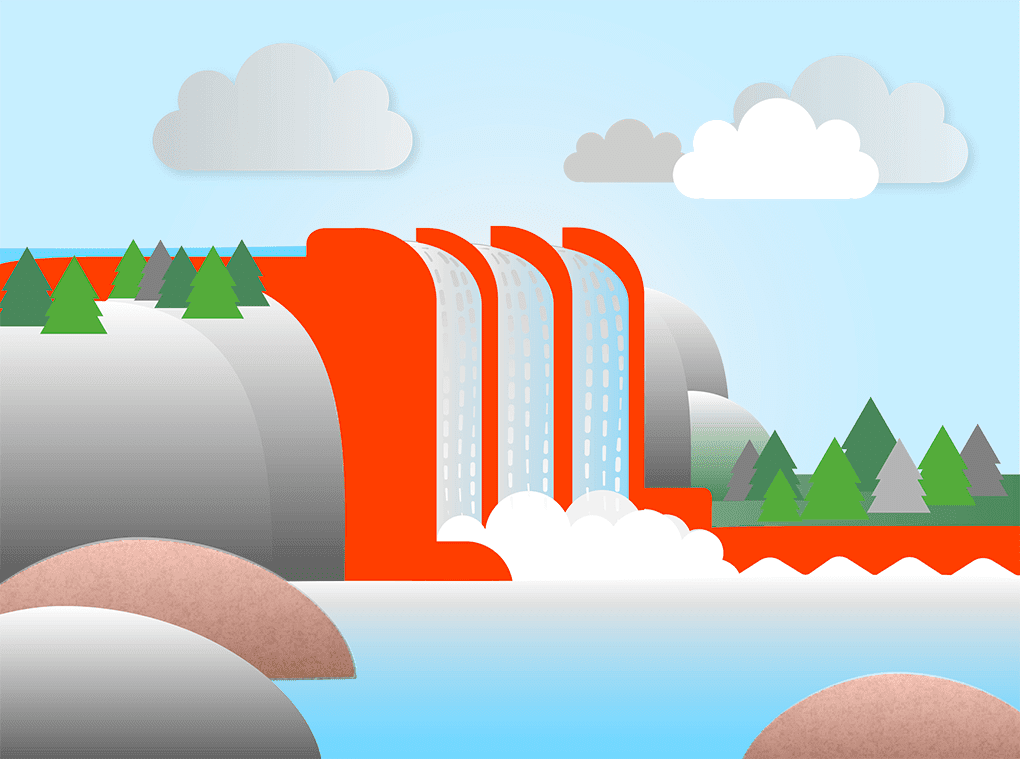
The challenge
Many of the small and medium-sized hydropower stations are in remote locations. Locations are dictated by nature, not only by the investment case, yet the return on investment is dependent on reliability and uptime. Therefore, in many cases, the know-how needed for condition monitoring and predictive maintenance is required to travel to the location. This leads to higher costs in the form of spare parts, logistics and labor, as well as compromises in terms of, e.g., how frequently inspections are performed.
Keep an eye on assets in modern means
Traditional on-line systems have not been developed with the aim of creating an agile remote condition monitoring solution, ending up being complex and costly. With Condence technology, we have scaled down the cost making it available for smaller sites and applications in remote locations without compromising quality and the depth and breadth of the analysis (see also Wind turbines). Instead of requiring frequent reporting intervals, with Condense, it is possible to receive a real-time trend of the condition of, for example, bearings. With Condense, everyone involved has the same information at their disposal. In the case that an external service provider is needed, they can access the data (also raw time-domain samples) from their office or monitoring center, avoiding the excess cost of travelling. Modern architecture and technology make monitoring simple, efficient and affordable.
A comprehensive view of machines health
Typical measurements of rotating machines are related to the data and analysis of oil and high-frequency vibration, complemented with measurements like temperatures or voltage. How extensive monitoring is implemented is, in many cases, dependent on the business case. Commonly the setup consists of vibration, oil-contamination and temperature measurements, which bring a view into the health of a machine and enables predicting of potential failures before they come become challenges. The modular system can always be updated later with additional sensors if needed. Measurements and analyses are controlled from the cloud.
The Benefits
Removing the element of surprise by merely knowing more and earlier is the first benefit of implementing the system. Once potential issues are detected, they can be followed, and actions optimized with condition-based maintenance methods instead of frequent inspections and time-based services. In this model, unplanned downtime for repairs can be minimized and performed when the loss of production has the least impact. Continuous monitoring builds trends and a database of raw data that can be used for further analysis, correlations with other parts of the operations, R&D and learning, all contributing to operational excellence.
The modern architecture of the Condense solution makes installing the system fast. Smart units and sensors can be configured remotely and data and analysis shared across the organization as needed.
For your service provider, this will also make inspections more efficient, reduce travelling and the need for spare part inventory as well.
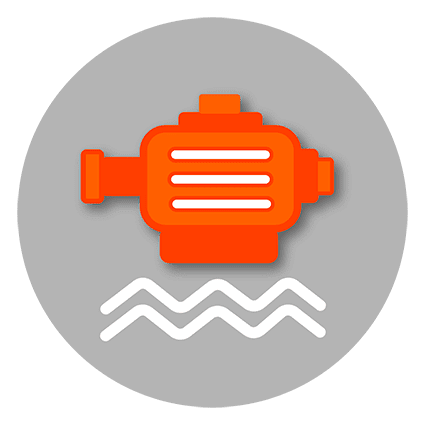
REMOTE PUMP STATION
Read more
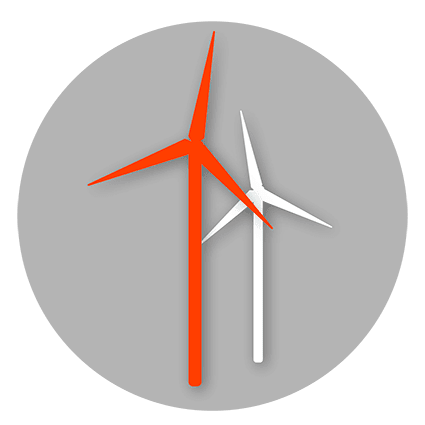
CONDENCE WIND POWER
Read more
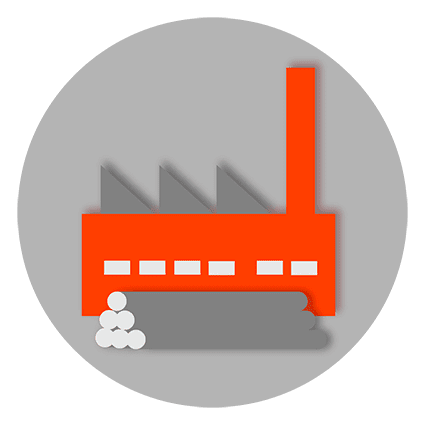
CONDENCE PULP AND PAPER
Read more
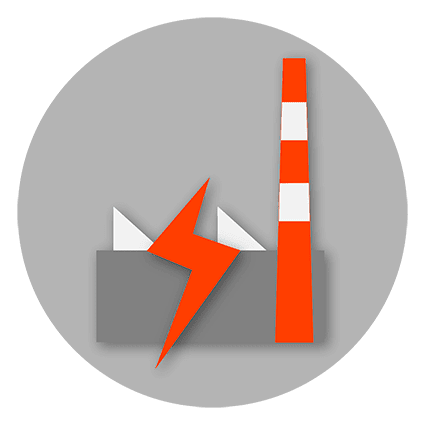
CONDENCE HEAT AND POWER
Read more
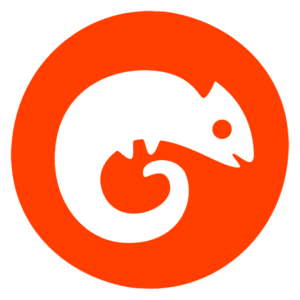
BACK TO INDUSTRIES
Read more
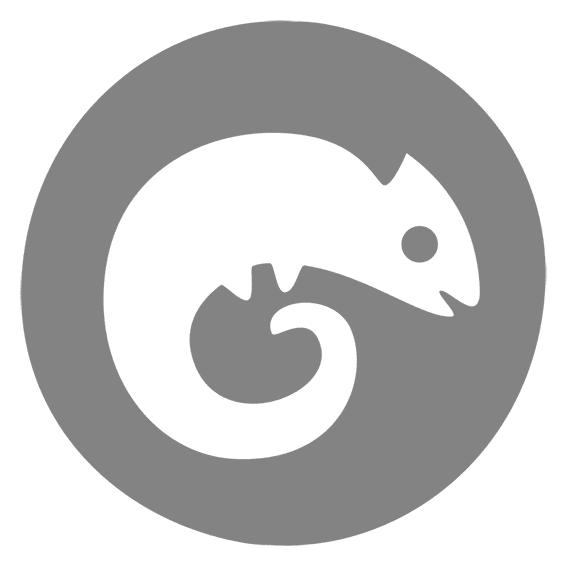
STEEL AND METAL
Coming soon...