Condition monitoring of
an electric motor
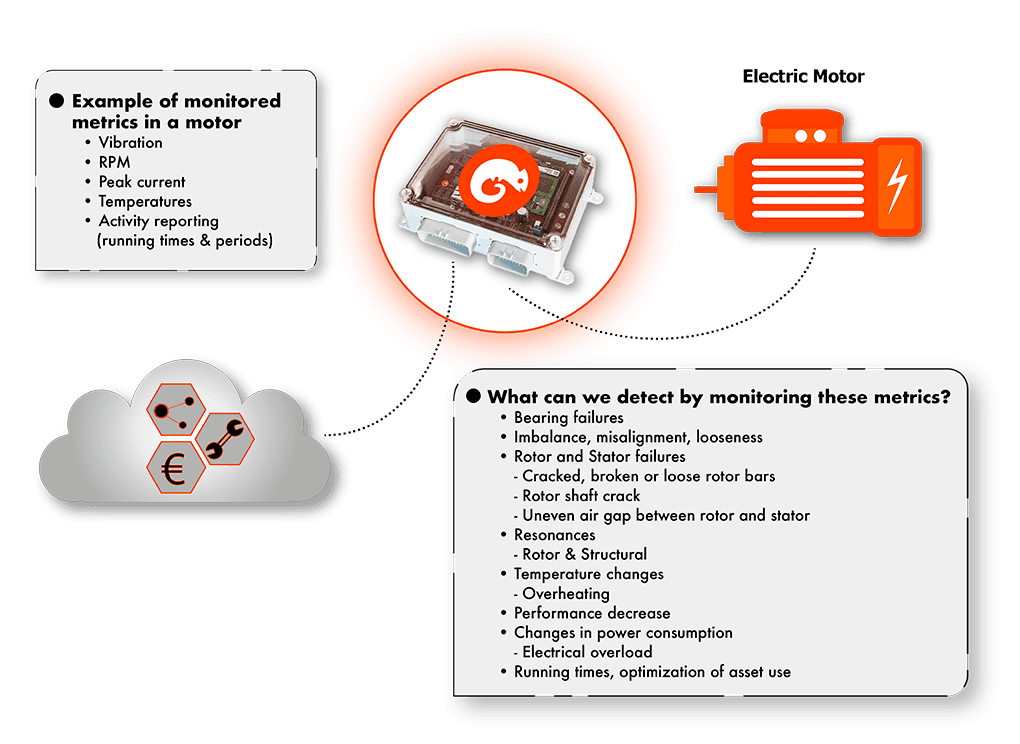
The challenge
Electric motors are critical in industrial production. Motor failure can lead to a complete machine breakdown, force the entire process to be shut down, causing production and financial losses. This makes electric motors critical components and underlines the importance of having an online condition monitoring system in place.
Simplifying the monitoring challenge
There are various failure modes, and, commonly, these failure modes are related to each other being the root cause or the symptom to one another. The motor can be mechanically overloaded, leading into electrical overload causing overheating. Bearings can wear down or may need more lubrication; the operational temperature or humidity can rise to the level where it damages the motor.
Most of the failure modes provide first indications before permanent damage has occurred. With Condence, one can combine several metrics and methods to build a comprehensive overview of motors health and prevent unnecessary surprises.
High-frequency vibration detects failures usually months in advance. E.g. by envelope analysis of acceleration and monitoring are known failure frequencies of bearings. Faults can be identified when they are microscopic in size or even before the damage when the lubrication needs attention, and there is plenty of time to react.
Managing temperature’s Electric motors are susceptible to overheating and overheating effects aggressively the lifespan of the motor. For example, every 10°C that the temperature of a motor rises, the insulation life reduced by 50%. Temperature, like other metrics, is easily and automatically monitored with Condence.
In addition to earlier mentioned, it is possible also to monitor the actual running hours of the motor and know how many hours you have left before the calculated end of life.
Automatic, online, and easy
With Condence, you can automatically detect early fault indicators, and once detected, automatically follow the trend of any calculated value, and set required alarms. Advanced analysis tools are at your disposal, anywhere and anytime. You avoid repeating frequent manual inspections, buy time to plan and react – in sum, increase operational excellence.
The implementation of Condence is made simple. In most cases, the installation does not require any interruption to the process. The configuration is done through the online user interface on the Condence web tool and firmware, new algorithms and other software updates are applied remotely.
Please use the links below to learn more about the Condence platform!
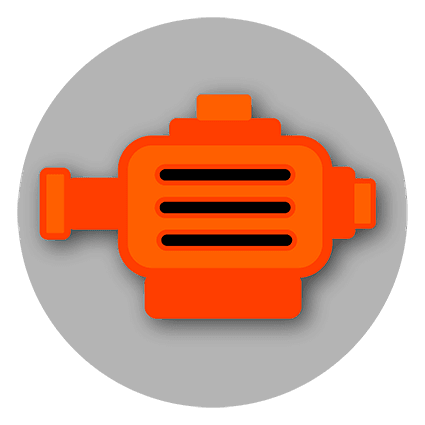
CONDENCE PUMP
Read more
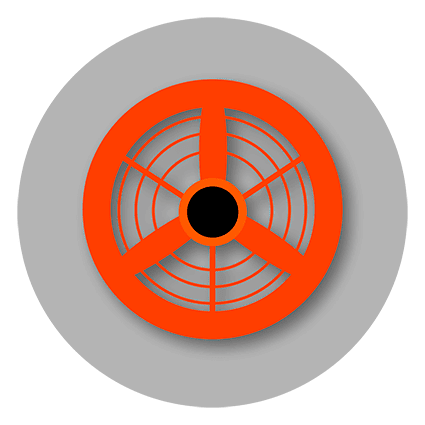
CONDENCE FAN/BLOWER
Read more
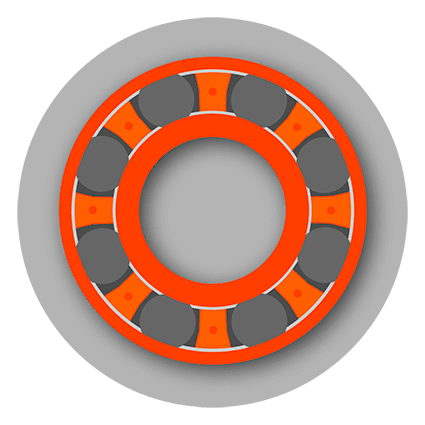
CONDENCE BEARINGS
Read more
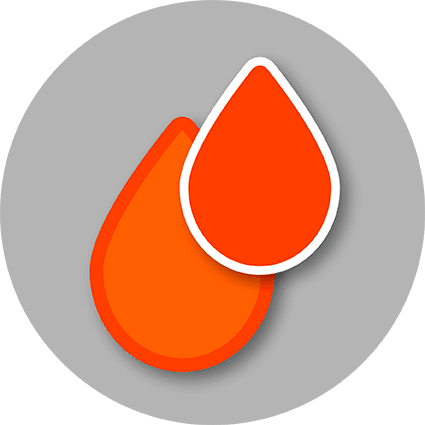
CONDENCE OIL
Read more
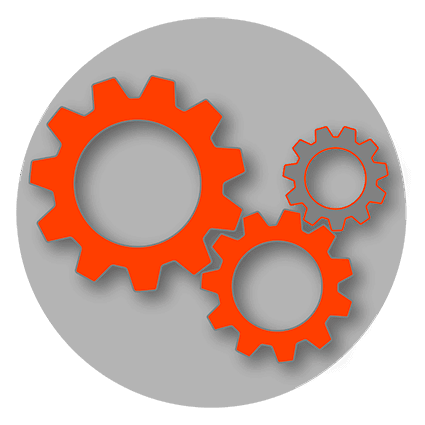
CONDENCE GEARBOX
Read more
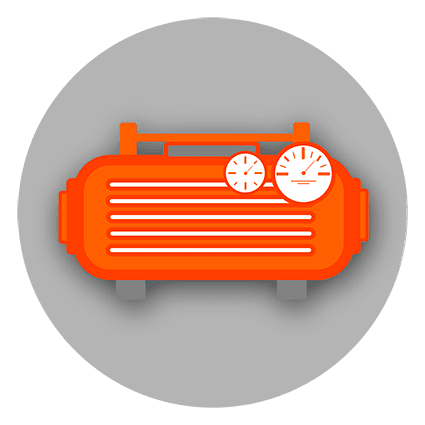
CONDENCE COMPRESSOR
Read more
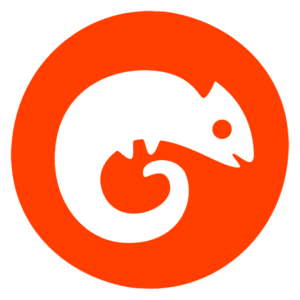
BACK TO APPLICATIONS
Read more
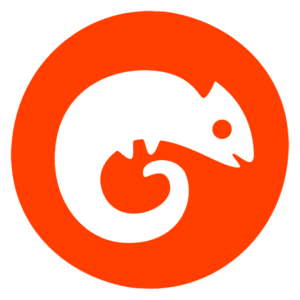
BACK TO PRODUCTS
Read more